Wszystko, co musisz wiedzieć o obrabiarkach
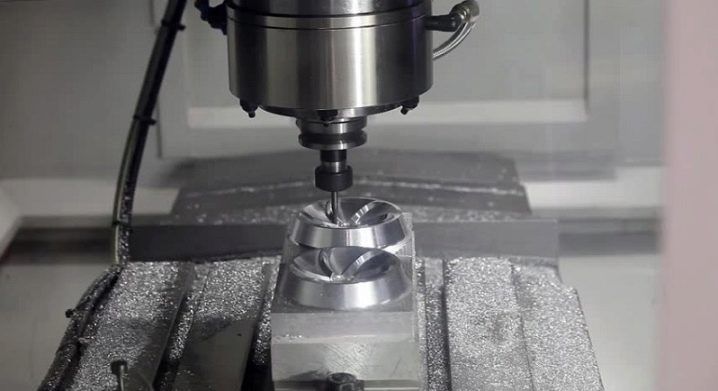
Żadna produkcja nie może obejść się bez obrabiarek. W takiej czy innej formie sprzęt do przetwarzania jest używany zarówno w dużych fabrykach, jak iw małych prywatnych firmach w dowolnym kierunku. Jednocześnie istnieje bardzo wiele klasyfikacji takich jednostek, każda z nich ma swoją własną funkcjonalność, opcjonalną zawartość, cechy techniczne i operacyjne.
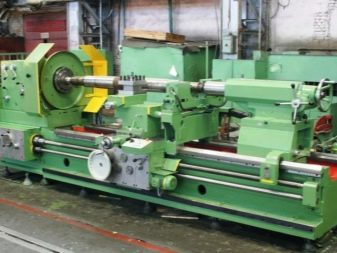
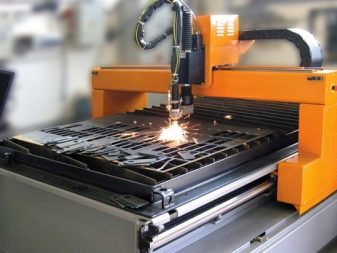
Co to jest?
Maszyny należą do grupy jednostek przemysłowych. Od wszystkich innych typów urządzeń technologicznych odróżnia je obecność łóżka, na którym zainstalowany jest główny organ funkcjonalny lub system bloków roboczych. Jako element obróbkowy może pełnić wiertło diamentowe, tarcza ścierna lub wiertło – zależy to bezpośrednio od rodzaju wykonywanych operacji. W większości przypadków maszyny wykorzystywane są w dużych zakładach przemysłowych.
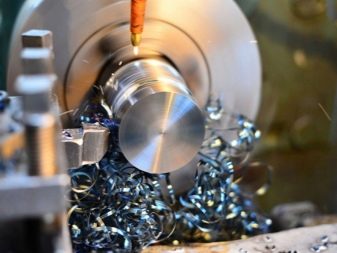
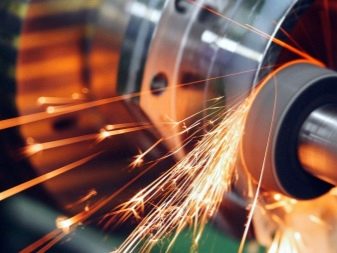
Oni reprezentują masywna konstrukcja zapewniająca platformę, zaciski, silnik i wiele innych elementów... W małych warsztatach i warsztatach domowych potrzebny jest bardziej kompaktowy sprzęt. W ostatnich latach wśród obrabiarek pojawiły się nie tylko urządzenia stacjonarne, ale również mobilne. Jednocześnie granica między mini-maszyną a narzędziem ręcznym czasami nie jest wyznaczana nawet przez producentów. Niemniej jednak to rama, obecność elektrowni i korpus obróbczy zaliczają jednostki do grupy obrabiarek. A które z nich rozważymy dalej.
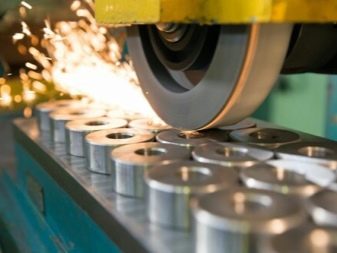
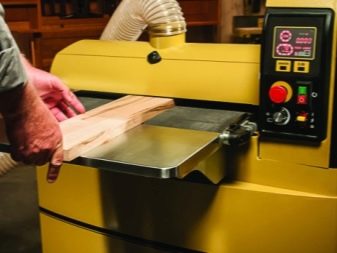
Opis gatunków
W dzisiejszych czasach poziom automatyzacji przedsiębiorstw przemysłowych stale rośnie, więc liczba maszyn sterowanych mechanicznie jest coraz mniejsza. Dlatego wszystkie maszyny można warunkowo podzielić na modele ręczne, półautomatyczne i automatyczne. Większość nowoczesnych instalacji jest sterowana numerycznie... Ten rodzaj kontroli zapewnia zwiększoną dokładność strojenia, a samo przetwarzanie odbywa się z minimalnym błędem. Główną zaletą maszyn CNC jest brak konieczności ciągłego monitorowania postępu produkcji, gdyż wszystkie główne parametry pracy ustawiane są przez operatora przed rozpoczęciem obróbki.
Specyfikacje maszyny różnią się w zależności od rodzaju przetwarzanego materiału. Większość typów jednostek służy do pracy z produktami drewnianymi i metalowymi. Jednocześnie w przypadku drewna dopuszczalne jest stosowanie jednostek o mniejszej mocy, ale z wyjątkową dokładnością strojenia. W przypadku przedmiotów metalowych moc musi być maksymalna. Istnieją różne rodzaje maszyn – żłobiarka, falcerka, szyno-krajarka, kantówka, korowarka, do falcowania, łuszczarka, precyzyjna, a także kopiująca i laserowa.
Najpopularniejsze to frezarki, wiertarki i tokarki.
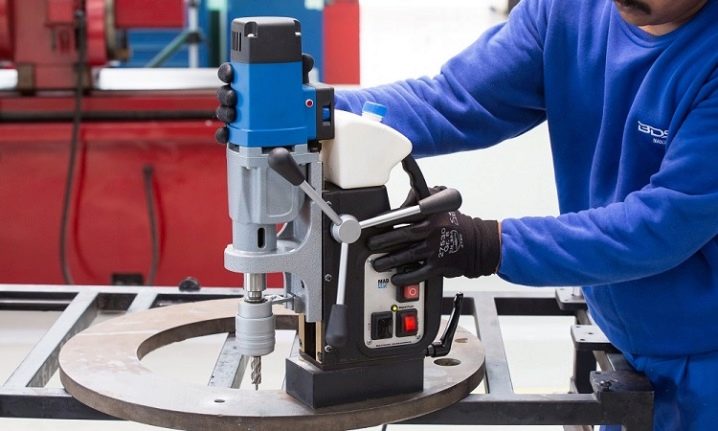
Cięcie metalu
Do pracy z metalem stosuje się maszyny do obróbki metalu, prostowania blach, maszyny do cięcia zbrojenia oraz instalacje do siatek. Wszystkie rodzaje obrabiarek do obróbki metali są podzielone na kilka kategorii.
- Obrócenie - wykonać obróbkę stale obracających się wewnętrznych i zewnętrznych powierzchni przedmiotu obrabianego. W takim przypadku podczas obróbki część obraca się wokół własnej osi.
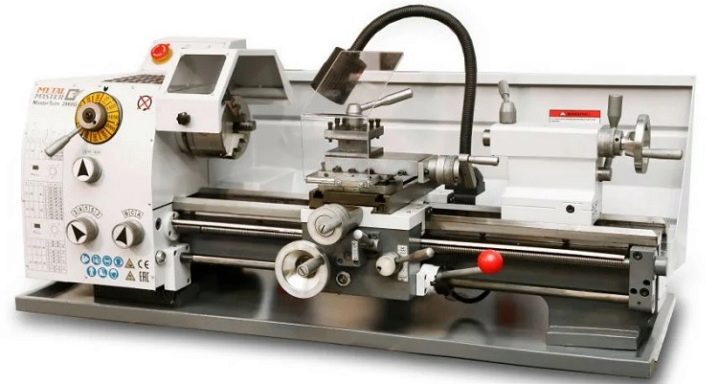
- Wiercenie - w zestawie znajdują się również wytaczarki, które są niezbędne, gdy zachodzi potrzeba formowania otworów ślepych i przelotowych.W procesie obróbki narzędzie obraca się jednocześnie z posuwem przedmiotu obrabianego, w mechanizmach wytaczarskich posuw odbywa się w wyniku ruchu podstawy roboczej.
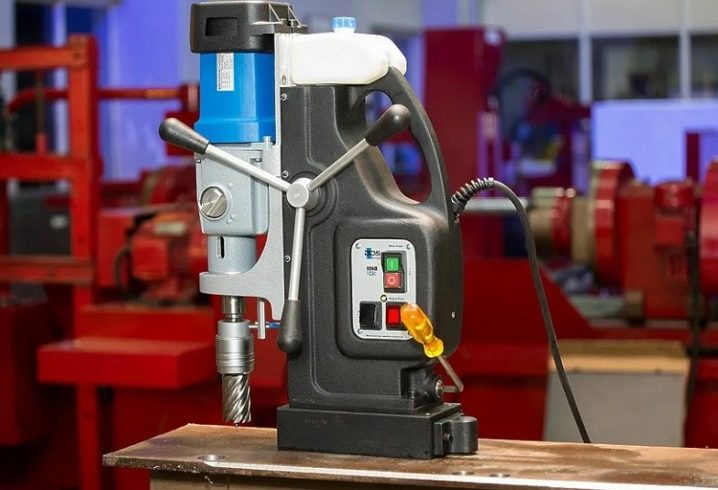
- Szlifowanie - obejmują kilka rodzajów maszyn. Wszystkich łączy obecność ściernicy jako podstawowego narzędzia pracy.
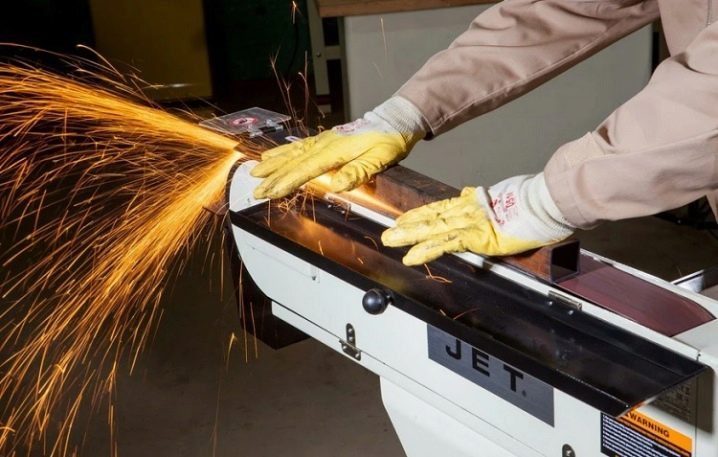
- Wykańczanie i polerowanie - stosuje się tu również tarczę ścierną. Wraz z pastą polerską wygładza powierzchnię.
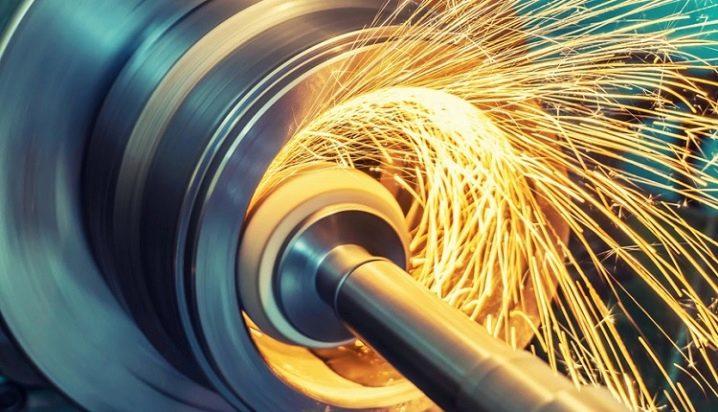
- Cięcie kół zębatych - przeznaczone są do projektowania uzębienia kół zębatych, można tu również przypisać szlifierki.
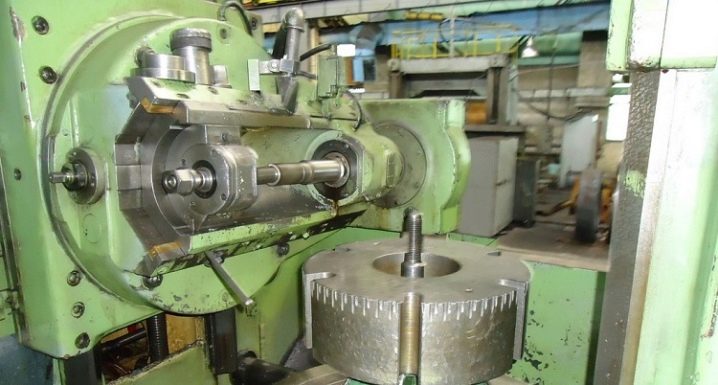
- Przemiał - w tej kategorii jako organ funkcjonalny używany jest frez wieloostrzowy.
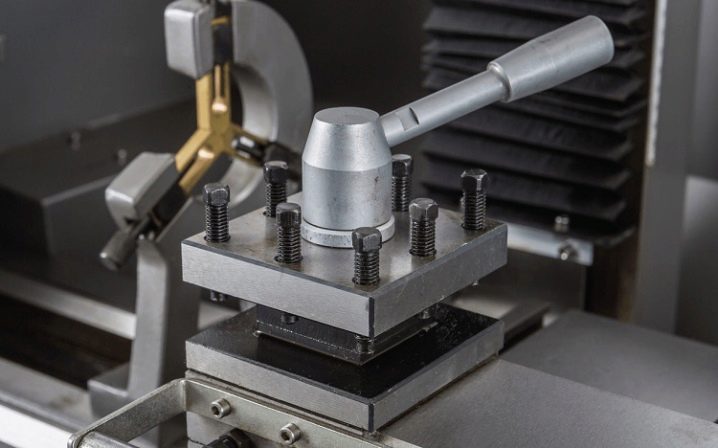
- Struganie - zasada działania tych modułowych urządzeń opiera się na ruchu posuwisto-zwrotnym przedmiotu obrabianego. Split - służą do oddzielania kątownika, kanału, pręta i innych rodzajów walcowanego metalu poprzez cięcie.
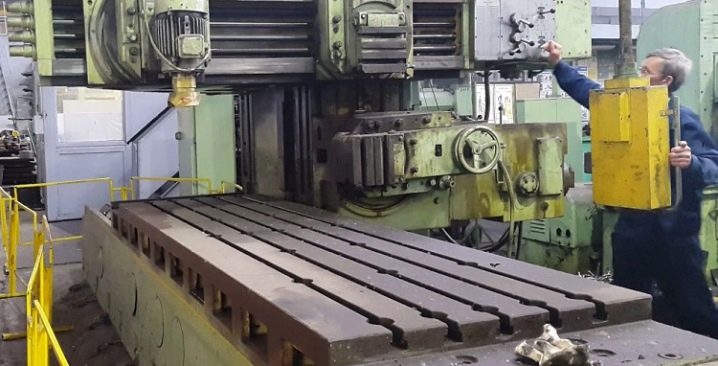
- Przewlekły - jako funkcjonalne narzędzie są tu zainstalowane przeciągacze wieloostrzowe.
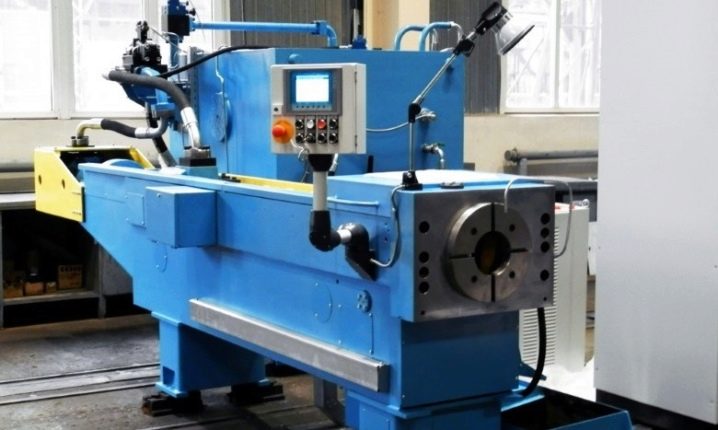
- Gwintowanie - w tej grupie znajdują się jednostki przeznaczone do gwintowania. Tokarki nie są tutaj uwzględnione.
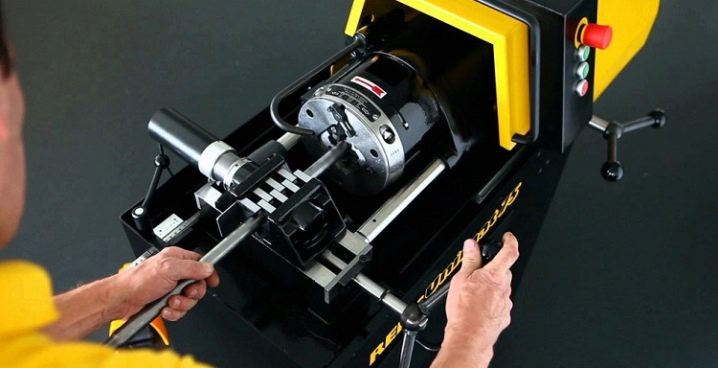
- Pomocniczy - w tej kategorii znajdują się dodatkowe instalacje umożliwiające wykonywanie pomocniczych operacji technologicznych.

Obróbka drewna
Nowoczesne maszyny do obróbki drewna dzielą się na kilka grup.
- Struganie - znane również jako struganie lub prościej strugarki. Ten sprzęt wykonuje dwa rodzaje manipulacji. Pierwszym z nich jest struganie podszewki i drewnianych wykrojów do określonej wielkości, czyli pogrubienia. Drugim jest wygładzenie powierzchni drewnianej poprzez struganie.
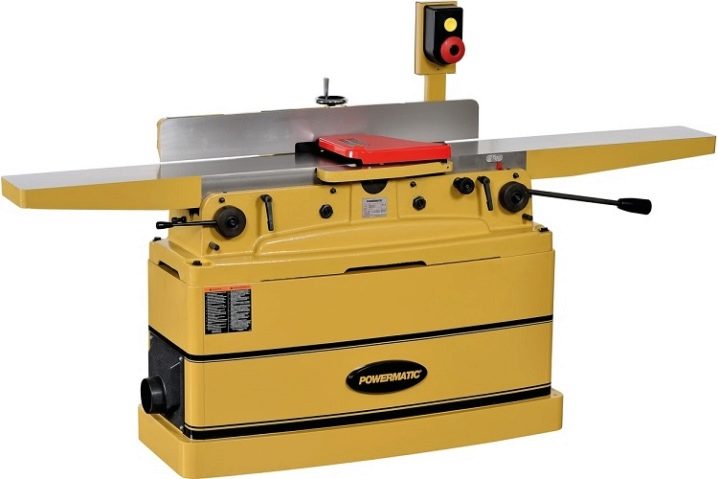
- Piły tarczowe - ten typ maszyny jest potrzebny, gdy konieczne jest cięcie przedmiotów obrabianych. Wyróżnia się maksymalną dokładnością w porównaniu z analogami.
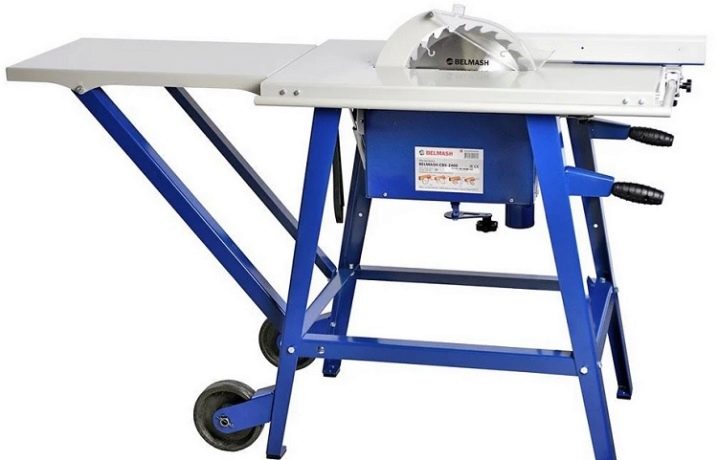
- Piły panelowe - umożliwiają wykonywanie cięcia poprzecznego i wzdłużnego, a także narożnego sklejki, tarcicy i półfabrykatów drewnianych, licowanych fornirem lub tworzywem sztucznym.
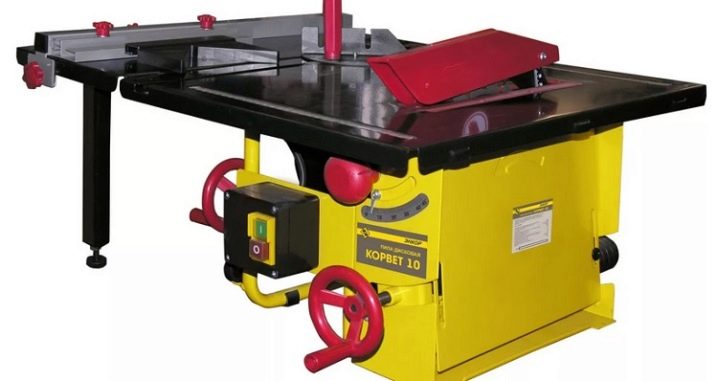
- Piłowanie - obejmuje to piły wzdłużne, piły tarczowe i traki ramowe. Służą do dzielenia masywnych przedmiotów na kilka mniejszych.
Wybór konkretnego rodzaju sprzętu uzależniony jest od parametrów twardości drewna.
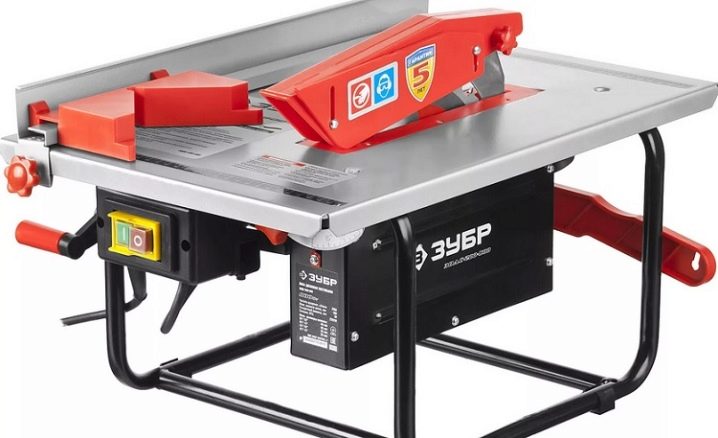
- Dłutowanie - taki sprzęt do obróbki drewna jest bardzo mocny. Dlatego podczas formowania perforacji lub rowków piłowania w obrabianych przedmiotach często dochodzi do zwiększonych obciążeń silnika maszyny.
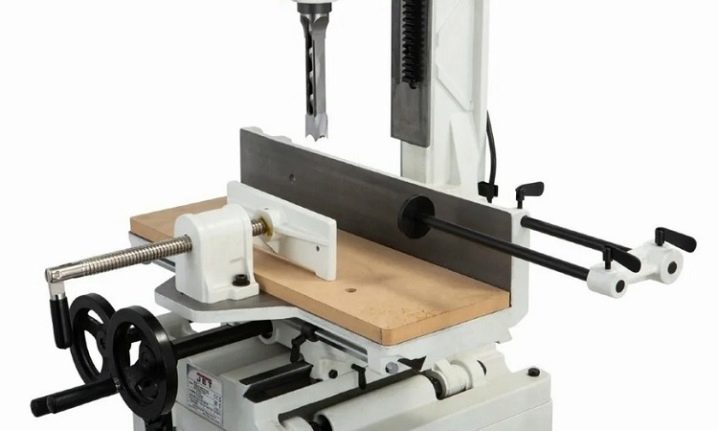
- Obrócenie - modele uniwersalne, wykorzystywane do prac w szerokim zakresie (wiercenie, gwintowanie, piłowanie rowków, toczenie).
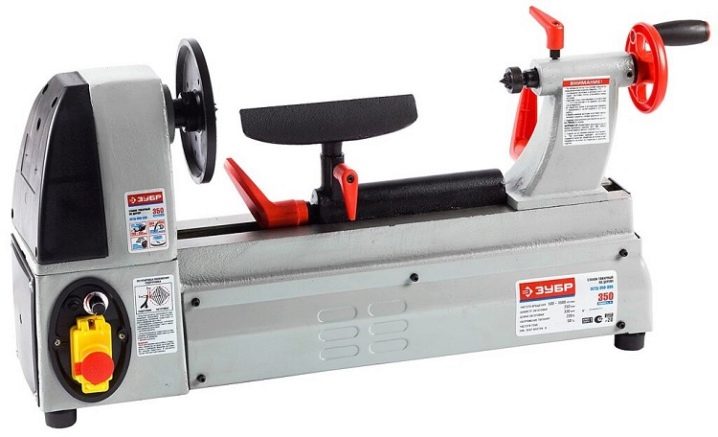
- Przemiał - podobnie jak w przypadku metalu, urządzenie to umożliwia obróbkę powierzchni wewnętrznych i zewnętrznych oraz płaszczyzn o różnych kształtach. Narzędzie jest poszukiwane do żłobienia zębów, służy również do tworzenia rowków.

- Wiercenie - jak sama nazwa wskazuje, narzędzie jest poszukiwane, gdy konieczne jest wykonanie otworów w drewnianych półfabrykatach.
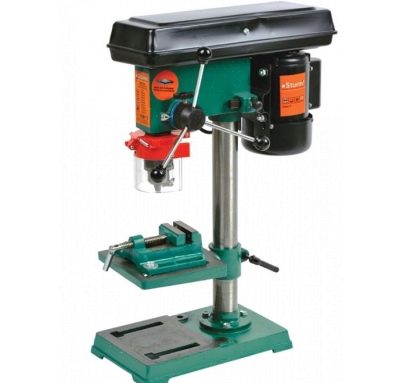
- Łączny - przeprowadzamy kompleksową obróbkę wyrobów stolarskich. Na przykład piłowanie, frezowanie i grubianie.
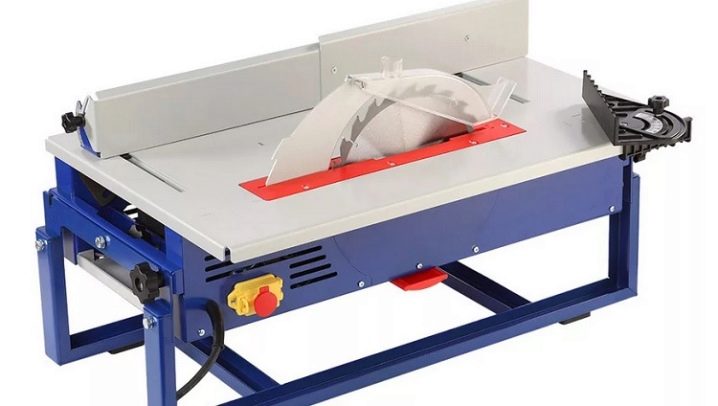
- Piły taśmowe - takie maszyny są pożądane przy cięciu półfabrykatów drewnianych o różnej twardości i wysokości. Pozwalają również na kręcone cięcie. Jest to opłacalny sprzęt, ponieważ zmniejsza ilość odpadów.
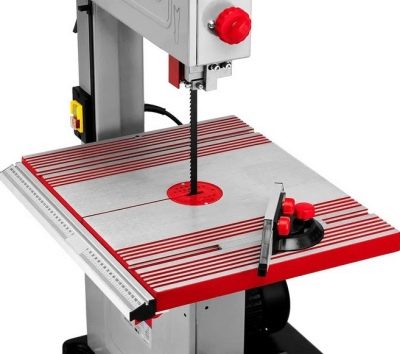
- Oklejanie krawędzi - takie jednostki pozwalają na ozdobną obróbkę krawędzi mebli i innych wyrobów z drewna.
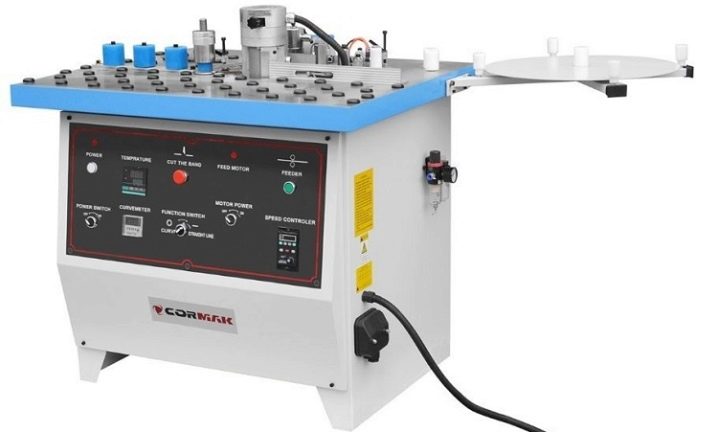
- Szlifowanie - precyzyjny sprzęt wykorzystywany na końcowych etapach rozwoju produktu. Usuwa wszelkie nierówności i niedoskonałości powierzchni, nadając produktowi estetyczny wygląd.
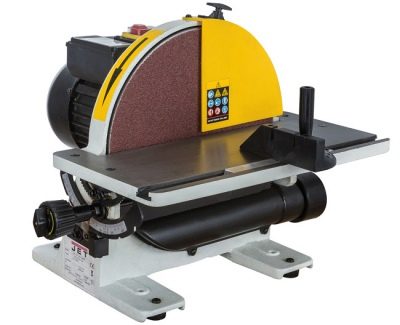
Cięcie kamienia
Konstrukcja maszyn do cięcia kamienia obejmuje łoże, a także zamocowane na nim narzędzie tnące... Ten ostatni napędzany jest silnikiem benzynowym lub elektrycznym, co zapewnia wysokiej jakości cięcie betonu, gresu porcelanowego, kamienia naturalnego i innych rodzajów supertwardych płyt. Sprzęt elektryczny wymaga podłączenia prądu przemiennego, ale nie emituje toksycznych spalin. Jednostki benzynowe są autonomiczne, ale rzadko używane, warunkiem ich działania jest dobrze wentylowane pomieszczenie robocze.
W zależności od rodzaju sterowania maszyny mogą być: ręczne i zautomatyzowane. Zautomatyzowane dzielą się na dwie grupy - przeznaczone do cięcia prostego i cięcia pod kątem 45 stopni oraz do cięcia kształtowego.
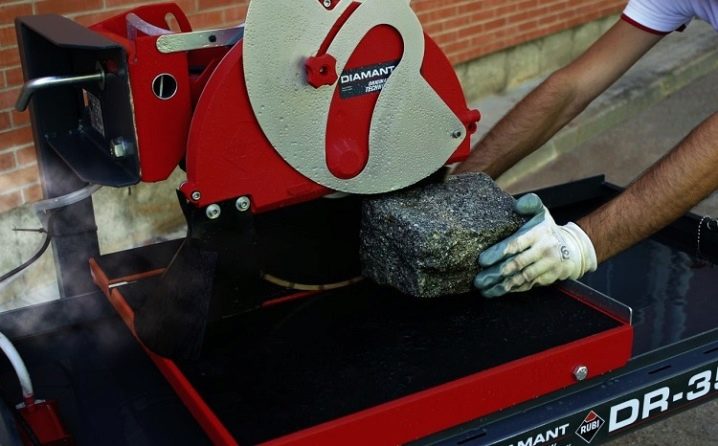
Pierwsza kategoria obejmuje:
- instalacje do łupania kamienia, - są poszukiwane w produkcji kostki brukowej i fragmentów dekoracyjnych, które są wykorzystywane do brukowania ulic i ścieżek ogrodowych;
- odpinany - odpowiadają za cięcie masywnych głazów na fragmenty o wymaganej wielkości;
- miernik - wyrównują powierzchnię kamienia i nadają mu estetyczny dekoracyjny wygląd.
Dostarczona funkcja obróbki pod kątem 45 stopni znacznie zmniejsza koszty pracy i znacznie skraca czas obróbki każdego przedmiotu. Figurowe cięcie odbywa się na specjalistycznym sprzęcie w celu nadania wyrobom wzorzystego kształtu.
Zasada działania takiego urządzenia oparta jest na technologii waterjet.
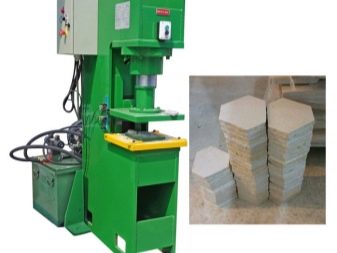
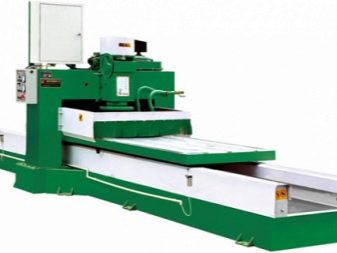
Inne
Wyróżniają się linie do przetwórstwa tworzyw sztucznych na granulat oraz maszyny do produkcji pelletu. Należą do nich urządzenia do rozdrabniania, czyszczenia, suszenia, separacji, granulacji i końcowego pakowania tworzyw sztucznych.
Jedna linia maszyn zawiera wszystkie powyższe mechanizmy. W niektórych przypadkach wymagany jest separator, stoły sortujące, przenośniki i przenośniki.
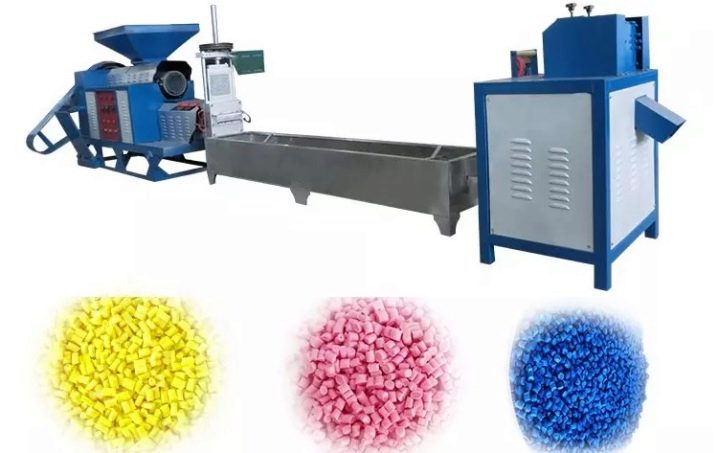
Klasy dokładności
Każdy typ obrabiarki podlega obowiązkowym kontrolom pod kątem zgodności z normami dokładności. Wyniki przeprowadzonych badań są odnotowywane w specjalnych aktach i umieszczane w paszporcie jednostki. Wszystkie typy sprzętu mają swój własny GOST, który reguluje maksymalne odchylenie dla każdej kontroli. Liczba i częstotliwość kontroli może się różnić w zależności od typu maszyny. Na przykład niektóre modele uniwersalnych frezarek CNC mogą zawierać kilkadziesiąt testów.
Zgodnie z wynikami badań cały osprzęt obrabiarki jest podzielony na klasy, biorąc pod uwagę dokładność pracy.
- h - instalacje o normalnej dokładności, służą do obróbki części z walcówki i odlewów.
- NS - zwiększona celność. Takie jednostki są produkowane na podstawie sprzętu o normalnej dokładności, ale ich instalacja odbywa się z najwyższą starannością. Maszyny te przetwarzają te same detale, ale cała praca jest wykonywana dokładniej.
- B / A - sprzęt o wysokiej i bardzo wysokiej precyzji. Tutaj zakłada się użycie specjalnych elementów konstrukcyjnych, dokładniejsze badanie jednostek i określonych warunków pracy.
- Z - szczególnie precyzyjne maszyny, pozwalają osiągnąć maksymalną precyzję obróbki detali. Są poszukiwane w produkcji narzędzi pomiarowych, kół zębatych i innych opcji przetwarzania.
Odchylenia z testów sąsiednich klas dokładności urządzenia różnią się od siebie w granicach 1,6 razy.
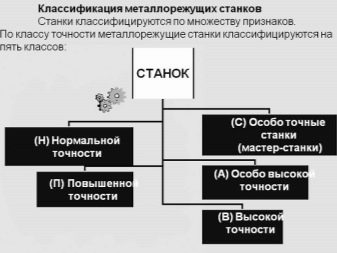
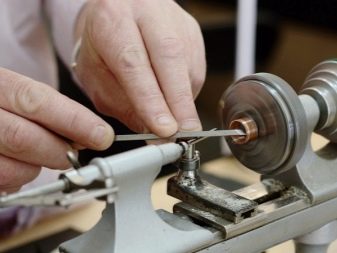
Zgodnie z GOST 8-82 dla wszystkich typów maszyn, w tym wersji CNC, wprowadzono ujednolicony standard badań dokładności. Zgodnie z nią o przynależności do kategorii decydują trzy parametry:
- dokładność geometryczna samego sprzętu;
- precyzyjna obróbka kawałków ciasta;
- Dodatkowe opcje.
Klasy dokładności są przypisywane do kategorii maszyn na podstawie tego standardu. W takim przypadku sprzęt należący do tej samej grupy musi zapewniać równą dokładność przetwarzania dla próbek o identycznej wielkości i kształcie.
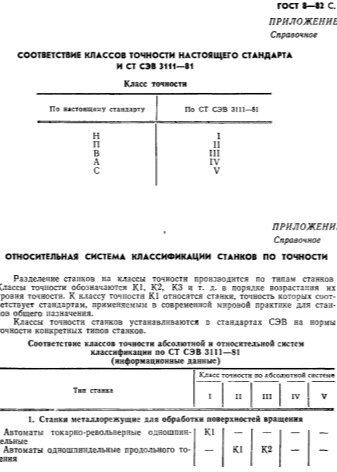
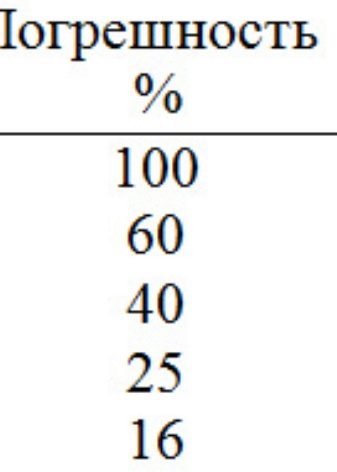
Najlepsi producenci
Niezawodne, funkcjonalne i trwałe maszyny produkowane są w różnych krajach. Najwyższej jakości importowany sprzęt produkowany jest w USA, Europie, a także w wielu krajach azjatyckich. W czołówce największych producentów znajduje się kilka znanych marek.
- TOYODA (Japonia). Firma ta została założona w 1941 roku jako filia Toyota Motor Corporation. Początkowo firma specjalizowała się w produkcji szlifierek do wałków, ale od lat 70-tych. W XX wieku producent zapoczątkował produkcję precyzyjnych centrów obróbczych do masowej produkcji. Dziś firma jest uznawana za lidera w produkcji jednostek CNC.
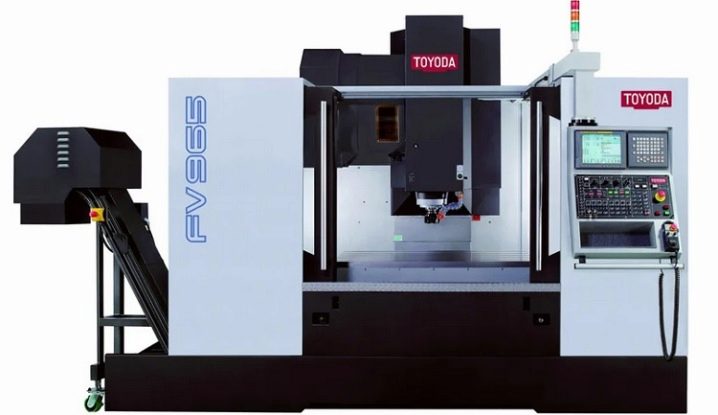
- SMTCL (Chiny). Fabryka obrabiarek uznawana jest za największą w Chinach, produkcja wyrobów przekracza 100 tys. szt. obrabiarek rocznie. Przedsiębiorstwo rozpoczęło działalność produkcyjną w 1964 roku. Do 2020 roku koncern obejmował 15 zakładów produkcji obrabiarek, a także ośrodek badawczy zajmujący się tworzeniem jednostek high-tech. Produkowane maszyny sprzedawane są w ponad 70 krajach świata, m.in. w Rosji, Włoszech, Niemczech, Anglii, Kanadzie, USA, a także w Turcji, Korei Południowej, Japonii i RPA.

- HAAS (USA). Amerykańskie przedsiębiorstwo działa od 1983 roku, dziś uważane jest za największą fabrykę obrabiarek w Stanach Zjednoczonych. Portfolio produktów obejmuje jednostki tokarskie, moduły obróbcze CNC oraz duże, pięcioosiowe specjalistyczne zakłady. Jednocześnie 75% wyposażenia sklepu stanowią maszyny własnej produkcji, takie podejście może znacznie obniżyć koszt produktów.
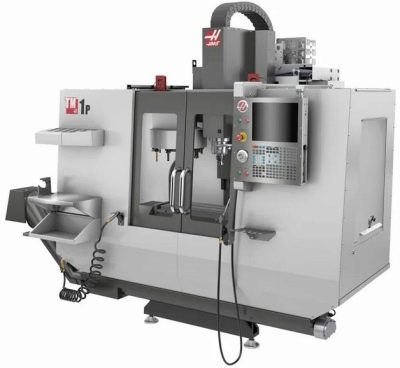
- ANCA (Australia). Producent produkuje szlifierki CNC od połowy lat 80-tych. XX wiek. Warsztaty znajdują się w Melbourne, dwie kolejne fabryki działają na Tajwanie i w Tajlandii. Firma produkuje maszyny do cięcia i ostrzenia narzędzi, instalacje do produkcji gwintowników oraz produkuje agregaty do frezowania i szlifowania.
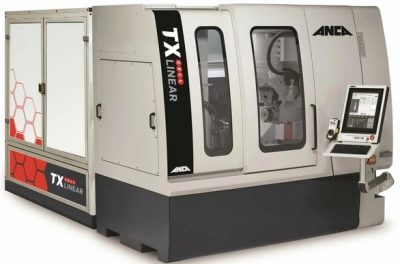
- HEDELIUSZ (Niemcy). Początek pracy niemieckiej firmy przypadł na rok 1967. Początkowo producent ograniczył asortyment maszyn do obróbki drewna. Ale dekadę później uruchomiono linię do tworzenia urządzeń obróbczych na potrzeby przemysłu metalowego.
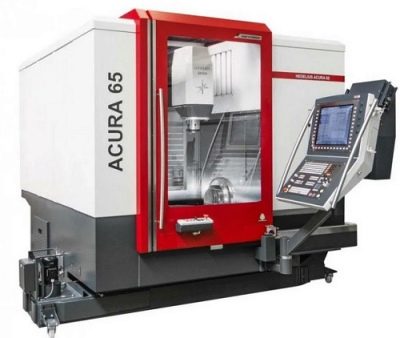
- Biglia (Włochy). Włoski producent jest uznawany za jednego z liderów w produkcji wydajnych tokarek. Działa od 1958 roku. W ofercie firmy znajdują się centra tokarskie i frezarskie, a także tokarki karuzelowe, instalacje do obróbki prętów okrągłych oraz instalacje do obróbki skrawaniem.
Jakość produktu potwierdzają międzynarodowe certyfikaty ISO 9001 oraz CE Mark.
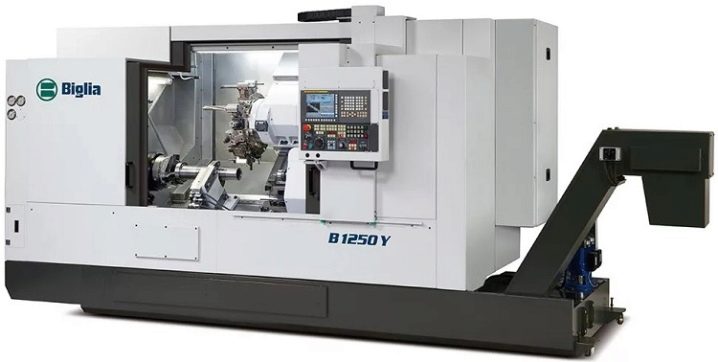
Komponenty i akcesoria
Wszystkie komponenty stosowane w maszynach można warunkowo podzielić na 3 kategorie.
- Mechaniczny - to są prowadnice, a także łożyska do nich. Dotyczy to również zębatek, pasów napędowych do przekładni, sprzęgieł, samotoków, skrzyń biegów i innych.
- Elektromechaniczny - obejmują wszelkiego rodzaju silniki, napędy wrzecion i osi. Do tej grupy należą silniki pomocnicze, np. do podawania chłodziwa. W kategorii znajdują się również zasilacze do ich sterowania (zasilacze, przemienniki częstotliwości, przekaźniki elektromagnetyczne, czujniki końcowe).
- Elektroniczny - ta grupa materiałów eksploatacyjnych składa się z płyt, łączności, sterowników i wielu innych.
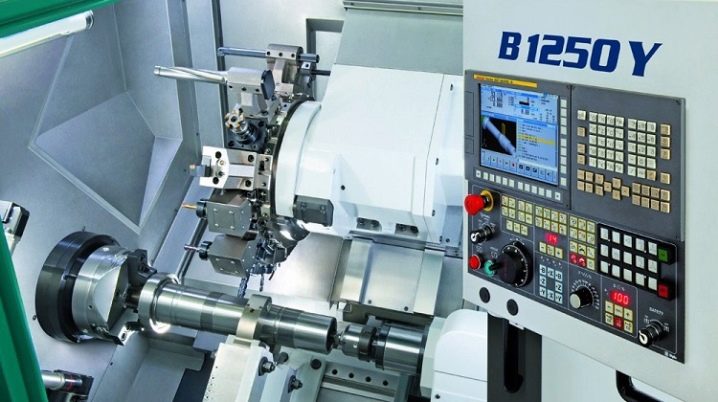
Należy pamiętać, że niektóre materiały eksploatacyjne tworzą ze sobą pojedyncze połączenie funkcjonalne... Przykładem są: silnik krokowy, sterownik i zasilacz do napędu. Wszystkie elementy tego pakietu muszą dokładnie do siebie pasować. To samo dotyczy grupy: wrzeciono, przetwornica częstotliwości, śruby i nakrętki, zębatka i zębnik.
W przypadku konieczności wymiany jednej z części zamiennych w takim zestawie, wyboru należy dokonać uwzględniając parametry techniczne i eksploatacyjne wszystkich pozostałych elementów. Wybierając jedną konkretną część zamienną z takiej grupy, konieczne jest dostarczenie sprzedawcy głównej dokumentacji dla pozostałych elementów pakietu. Muszą mieć co najmniej jednego producenta.

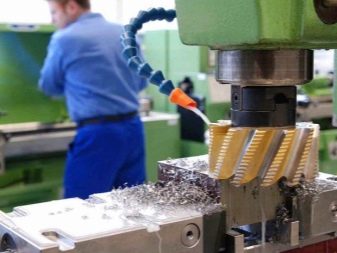
Niuanse naprawy
Naprawa obrabiarek nie jest łatwym procesem. Zrób to sam mogą zrobić osoby posiadające specjalistyczne umiejętności pracy z takim sprzętem. Oto przykład na tokarce. Nie jest tajemnicą, że chęć wyposażenia warsztatu w tokarkę często kłóci się z budżetem. Dlatego niektórzy kupują używane modele, czasami w dość opłakanym stanie.
Naprawy pozwalają wydłużyć żywotność takiego sprzętu. Jedną z najczęstszych wad takich maszyn jest zubożenie powierzchni skrawających maszyny do obróbki metalu, prowadzące do zużycia. W takim przypadku naprawa musi koniecznie obejmować procedurę skrobania, w wyniku której usuwane są wszystkie uszkodzone warstwy powierzchni ciernych.
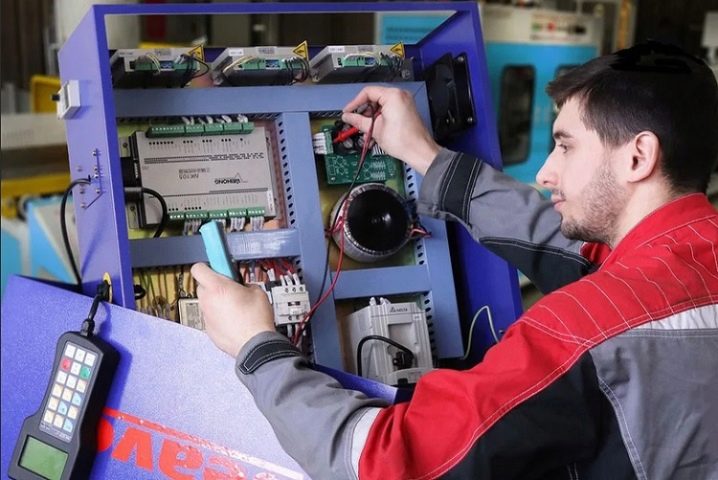
Najczęściej suwmiarki, suporty i prowadnice łoża podlegają skrobaniu na tokarkach. Rozwój prowadnic wiąże się z częstym wnikaniem wiórów metalowych lub rażącym naruszeniem warunków pracy. Nagła zmiana trybów pracy, niewystarczające smarowanie i inne czynniki prowadzą do awarii. Skrobanie może być szorstkie - jest produkowane w celu wyeliminowania wyraźnych wad, w tym przypadku usuwa się 0,001-0,03 mm metalu.
Zaraz po obróbce zgrubnej wykonuje się drobne skrobanie, co pozwala zneutralizować wszelkie drobne nierówności identyfikowane z farbą. Pozostające na powierzchni plamy po zeskrobaniu nałożonej farby stają się przewodnikiem dla mistrza - im mniejsza jest ich liczba i średnica, tym gładsza będzie powierzchnia. W końcowej fazie prac wykonuje się skrobanie wykańczające, którego celem jest zapewnienie równomiernego rozprowadzenia plam.
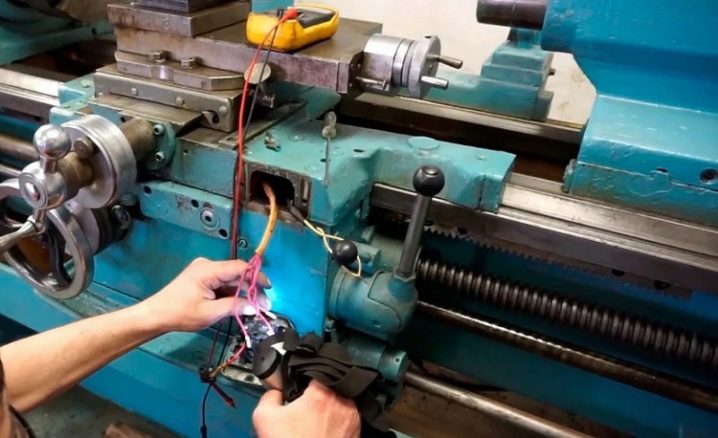
Oczywiście naprawy nie ograniczają się do skrobania. Jednak to właśnie ta miara pozwala zapewnić maksymalną dokładność skrętu i płynny ruch mechanizmów roboczych sprzętu.
Musisz to jednak zrozumieć każda naprawa maszyn zrób to sam jest wskazana tylko wtedy, gdy mówimy o lekkich, mało funkcjonalnych urządzeniach gospodarstwa domowego. Jeśli konieczne jest odtworzenie instalacji klasy średniej lub ciężkiej o wadze kilku ton, lepiej przekazać sprzęt w ręce specjalistów. Nie tylko przywrócą jej zdolność do pracy, ale także zwiększą produktywność.
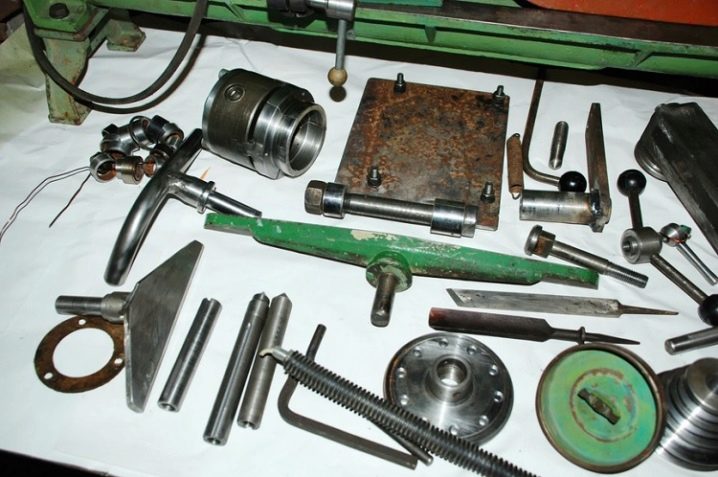
Komentarz został wysłany pomyślnie.