Wszystko o okruchach gumowych płytek

Drobno mielone płytki gumowe mają wyjątkowe właściwości. Pod względem komfortu, bezpieczeństwa użytkowania i estetycznego wyglądu po prostu nie ma konkurencji wśród materiałów do pokrywania przyległych terenów, boisk sportowych i wielu innych.
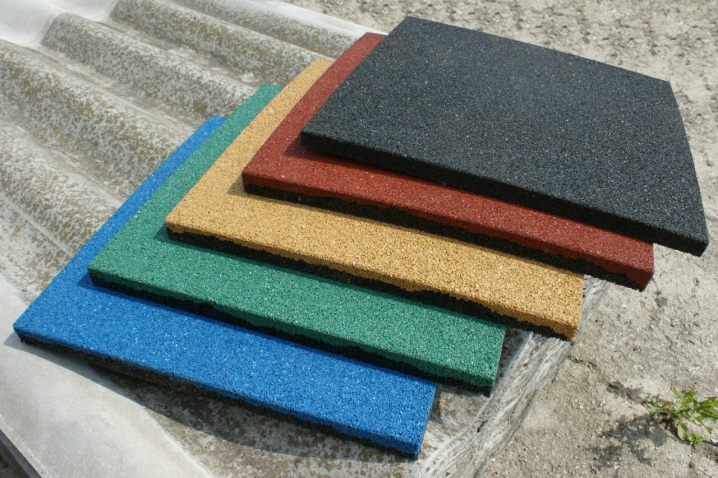
Zalety i wady
Powszechne stosowanie okruchów gumowych płytek wskazuje, że ma ogromny zakres zalet i doskonałe właściwości użytkowe. Jak każdy materiał ma swoje plusy i minusy.
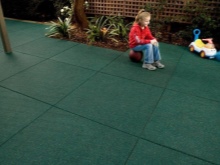


Rozważ pozytywy.
- Zróżnicowany asortyment kolorów, który pozwala udekorować witrynę w dowolnym stylu.
- Panele dostępne są w różnych wersjach - przepuszczającej wodę i wodoodpornej. Dzięki temu można go układać zarówno wewnątrz, jak i na zewnątrz.
- Wysoka trwałość produktów z okruchów gumowych pozwala na ich intensywne użytkowanie przez co najmniej 5 lat, a w normalnych warunkach - co najmniej 15 lat.
- Bezpieczeństwo i zmniejszenie kontuzji w sporcie. Gumowe panele są sprężyste, a w przypadku upadku ryzyko kontuzji jest znacznie mniejsze niż na innych rodzajach nawierzchni. Dzięki tej właściwości są głównym materiałem do aranżacji placów zabaw i boisk sportowych.
- Bezpieczeństwo środowiskowe płyt z okruchów gumy. Do produkcji wykorzystywane są materiały nieszkodliwe dla człowieka, dzięki czemu można je wykorzystać do niemal każdej potrzeby.
- Gumowa osłona ma działanie antypoślizgowe, co znacznie zmniejsza ryzyko kontuzji podczas lodu, śniegu czy deszczu.
- Montaż i demontaż płytek nie jest trudny do przeprowadzenia. Można go łatwo wyjąć i schować w innym pożądanym miejscu, nie tracąc kształtu i niezawodności produktów.
- Taka płytka dobrze radzi sobie z niekorzystnymi warunkami atmosferycznymi w postaci mrozu, opadów, nagłych zmian temperatury i innych, zachowując przy tym swoją wytrzymałość i estetyczny wygląd.
- Nie jest wymagany żaden specjalny wysiłek, aby wyjść. Wystarczy go umyć dowolnym detergentem, a znów będzie wyglądał jak prosto ze sklepu.
- Nie ma specjalnych wymagań dotyczących transportu.
- Ponieważ gumowa powłoka jest wysoce odporna na promienie UV, przez bardzo długi czas będzie wyglądać jak nowa.
- Produkcja wykorzystuje stare gumowe opony, co pozwala na ich masową utylizację, jednocześnie czyszcząc środowisko. To duży krok w kierunku ochrony przyrody.



Przejdźmy teraz do punktów ujemnych. Jak wszystkie produkty na bazie gumy, panele te dobrze się palą. Ale ponieważ w większości przypadków są one używane do powłok zewnętrznych, czynnik ten nie jest tak istotny, aby odmówić ich użycia.
Kolejną wadą jest dość wysoki koszt. Cena zależy od wielu niuansów, takich jak grubość, kolor, komponenty i inne czynniki.
Jeśli porównamy listę zalet i wad, drugi jest znacznie mniejszy. To sprawia, że płytki z okruchów gumy są bardzo popularne, aw niektórych obszarach po prostu niekwestionowane.



Metody produkcji
Aby wykonać płytki z okruchów gumy, potrzebujesz specjalnego sprzętu i pomieszczeń.Ten ostatni powinien mieć powierzchnię co najmniej 100 m2, a ponadto ogrzewany – w okresie chłodnym temperatura w nim nie powinna spaść poniżej +5 stopni Celsjusza.
Główny nacisk kładziony jest na sposoby wytwarzania płyt gumowych. Początkowa kwota, która będzie wymagana do uruchomienia, będzie zależeć od ich jakości i mocy. Możesz kupić wszystko osobno, ale lepiej kupić kompletną linię jako zestaw. Ułatwi to i ujednolici proces.

Teraz oferowane są różne zestawy, ale przynajmniej będziesz potrzebować:
- mikser - do mieszania różnych składników;
- piece - do suszenia produktów;
- prasa hydrauliczna - do formowania produktów;
- formularze;
- przewód - do wybijania otworów do łączenia elementów;
- stół do formowania i stojak do mocowania.
To najbardziej niezbędny sprzęt do wdrożenia produkcji. Z jego pomocą można już rozpocząć produkcję powłok na bazie okruchów gumy o różnych grubościach i rozmiarach.



Obecnie płyty wykonuje się trzema różnymi metodami.
Przeziębienie
Ta metoda jest uważana za klasyczną, została opracowana przez pierwszego i jest już uważana za przestarzałą.
Proces składa się z 2 etapów. Mieszankę dokładnie wymieszaną w mikserze rozlewa się do wybranych form, umieszczonych na specjalnym stole. Następnie następuje prasowanie pod wysokim ciśnieniem (ok. 5 ton) i przeniesienie do pieca suszarniczego, gdzie w temperaturze 55-60°C produkty są suszone przez co najmniej 6 godzin. Następnie formy są demontowane - i produkt jest gotowy do użycia.
Ta metoda ma następujące zalety: sprzęt jest powszechny i dostępny, a płytki można produkować na małą skalę.
Wady to konieczność ciągłego monitorowania procesu, dość duży procent wad i wysoka cena.

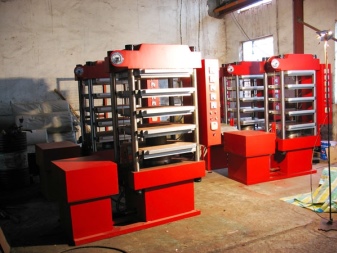
Gorący
Za najbardziej postępową uważa się metodę prasowania na gorąco. Pierwszy etap pokrywa się z poprzednią metodą, a różnica polega na prasowaniu paneli. Przygotowaną kompozycję umieszcza się w metalowych formach, podgrzewa do temperatury + 120 ... 220 ° C i jednocześnie prasuje.
W oparciu o parametry produktu proces trwa od 3 do 20 minut. W tym czasie klej rozprowadza się równomiernie na mieszance, tworząc bardziej niezawodne połączenie między okruchami gumy. Technologia ta umożliwia uzyskanie płytek o lepszych właściwościach niż metodą na zimno.
Zalety: szeroka gama produktów, niski koszt, doskonała jakość paneli oraz niewielki procent wad produkcyjnych.
Są też wady: sprzęt jest dość drogi, a pracownicy muszą mieć odpowiednie kwalifikacje.


Termochemiczny
To najnowsza metoda, która pozwala uzyskać produkty spełniające wszystkie wymagania, nawet te najbardziej rygorystyczne. Różnica w stosunku do dwóch pierwszych technologii polega na tym, że w razie potrzeby można ustawić wymagane parametry. Innymi słowy, produkty z tego samego materiału mogą mieć różne wskaźniki gęstości, twardości, elastyczności i innych parametrów.
Proces przebiega tak:
- zmiażdżoną gumę miesza się z klejem;
- w zależności od wymagań do paneli dodawane są niezbędne komponenty;
- umieszczanie w formach, podgrzewanie i prasowanie (może trwać od 2 do 10 minut).
Po zakończeniu otrzymujemy produkty najwyższej jakości, gotowe do użycia.
Zalety są takie same jak w przypadku metody na gorąco, plus możliwość wytwarzania specjalistycznych rodzajów powłok. Wady również się pokrywają, a ponadto trzeba stale monitorować proces produkcji ze szczególną uwagą.


Co się dzieje?
Płytki z okruchów gumy różnią się grubością, rozmiarem i kształtem. Najpopularniejsze to prostokątne lub kwadratowe, ale dostępne również w postaci „kostek brukowych”. Czasami można znaleźć egzotyczne rodzaje gumowych paneli w postaci „puzzli”, wyposażonych w specjalne zapięcia na całym obwodzie.
Kształt nie wpływa na parametry płytek gumowych, dlatego warto wybrać go pod kątem przyszłego przeznaczenia.
Powierzchnia paneli może być gładka lub ryflowana, o różnych wzorach, co oprócz efektu antypoślizgowego, pozwala nadać chodnikowi lub chodnikowi niecodzienny wygląd.
Istnieje wiele rozwiązań kolorystycznych, a najpopularniejsze kolory to brązowy, czarny, terakota, czerwony, żółty, zielony.


Wymiary i waga
Wszystkie okruchy gumowe są produkowane zgodnie z TU 2533-001-0171450779-2012, która zawiera wszystkie wymagania dotyczące produktów. Wymiary paneli mogą być zróżnicowane, występują od 200x100 mm do 1000x1000 mm, o różnej grubości i gramaturze.
Najbardziej poszukiwane płytki to 500x500 mm. W zależności od grubości umieszcza się je na twardej powierzchni (10-30 mm) lub na luźnym podłożu (40-45 mm) na zewnątrz.
Wymiary, mm | Waga (kg |
500x500x10 | 2,25 |
500x500x16 | 3,5 |
500x500x20 | 4,25 |
500x500x30 | 6,4 |
500x500x40 | 7,4 |
500x500x45 | 8 |

Wszystkie płytki gumowe mogą być stosowane zarówno jako chodniki, jak i ścieżki ogrodowe, a także doskonale sprawdzają się jako wykładzina ulic na podwórkach.
Technologia układania
Taki materiał układa się na kilka sposobów.
Płyty o grubości 40 i 45 mm montowane są na podstawie wykonanej z materiałów sypkich. Proces jest bardzo podobny do układania konwencjonalnego betonu. Aby to zrobić, przygotuj poduszkę z piasku i żwiru o grubości 10 cm, bardzo dobrze ją ubij. Obwód torów lub terenu jest oznaczony ramką wykonaną zarówno z gumy, jak i betonu. Następnie układane są płyty. Panele są połączone ze sobą specjalnymi zamkami.
Montaż na solidnej podstawie przystosowanej do paneli o grubości 6-45 mm za pomocą kleju poliuretanowego. Podłoże jest oczyszczone z kurzu. Przed przyklejeniem do powierzchni podłoże jest zagruntowane. Klej nakłada się szpachelką, następnie klei się płytki zaczynając od środka.
Po instalacji musisz odczekać około 48 godzin - w tym czasie chodzenie po panelach jest niepożądane. A także należy zadbać o to, aby podczas montażu powietrze nie dostało się pod płytki. Jeśli nagle tam dotarł, możesz go usunąć, mocno dociskając produkt od środka do krawędzi.
Instalując na solidnej podstawie, musisz pomyśleć o nachyleniu, aby woda nie pozostała na powierzchni.
Przy układaniu na ziemi nie jest wymagane nachylenie - woda w naturalny sposób spłynie przez płytki, a następnie poprzez drenaż do gruntu.


Możesz dowiedzieć się, jak wybrać odpowiednią gumową płytkę z okruchów z poniższego filmu.
Komentarz został wysłany pomyślnie.