Maszyny do polerowania: rodzaje i wskazówki dotyczące ich użytkowania
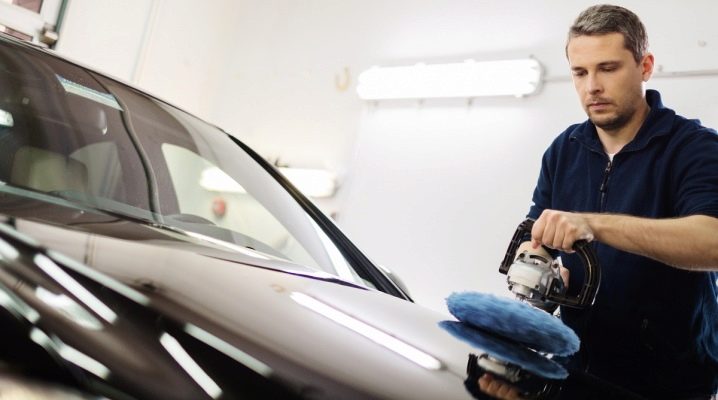
Nie wystarczy wykonać lub naprawić wiele produktów lub powierzchni. Konieczne jest również nadanie im charakterystycznego błyszczącego wyglądu, połysku. W tym celu często używane są specjalne urządzenia.
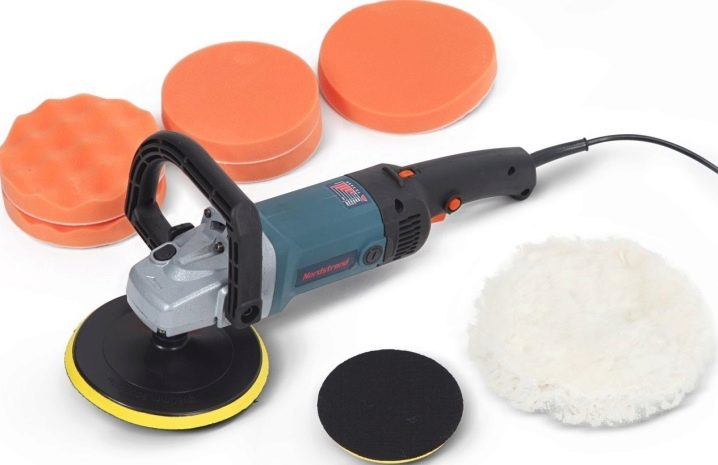
Osobliwości
Maszyna do polerowania może być używana w wielu różnych dziedzinach. W szczególności urządzenie to służy do wykańczania i poprawiania wyglądu powierzchni. Szeroką funkcjonalność narzędzia zapewnia zmiana dysz i past. Zadania takie jak:
- nadanie połysku lustra lub szyby okiennej;
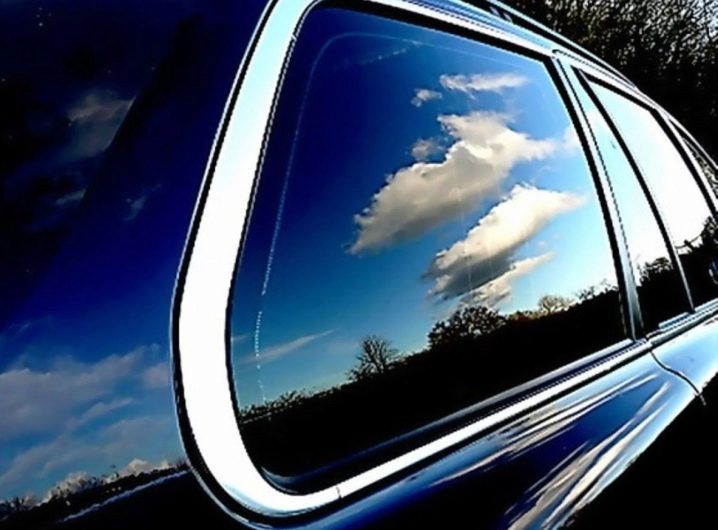
- poprawa wyglądu samochodu;
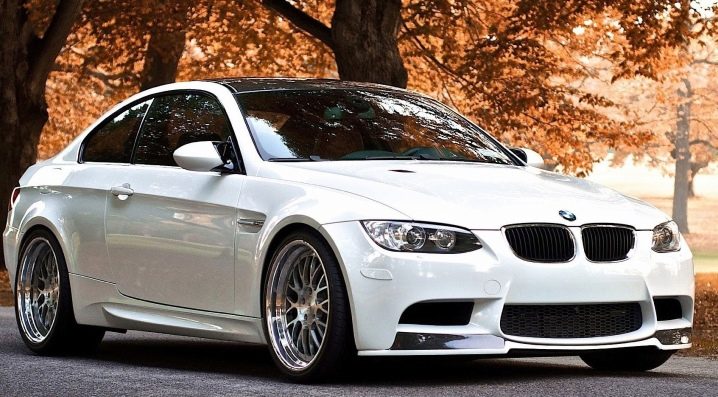
- polerowanie wyrobów z drewna.
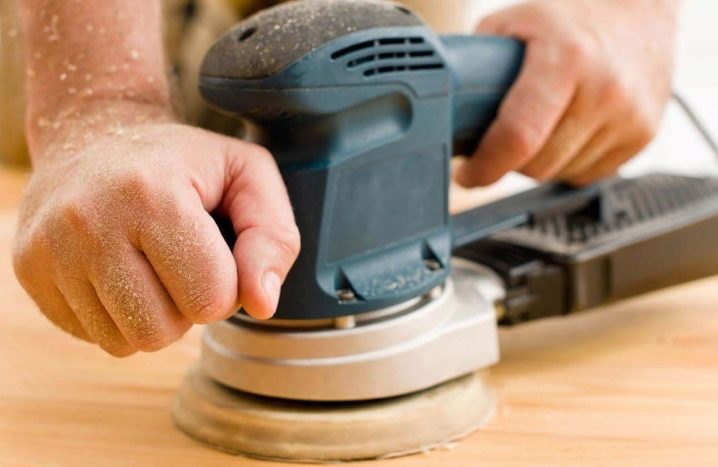
Bez względu na to, jakie zadanie jest rozwiązywane, polerka ma dość typową budowę:
- rama;
- mechanizm napędowy;
- para uchwytów;
- zdejmowana tarcza polerska.

Wygląd takiego urządzenia jest podobny do szlifierki kątowej. Jednak duża różnica polega na zastosowaniu zupełnie innych płyt. Naturalne jest, że wraz ze wzrostem wielkości części roboczej zwiększa się również przetwarzana powierzchnia. Ważnymi cechami maszyn polerskich są również wielkość ziarna zainstalowanych tarcz oraz całkowita moc urządzenia. Wraz ze wzrostem parametrów technicznych rośnie cena.
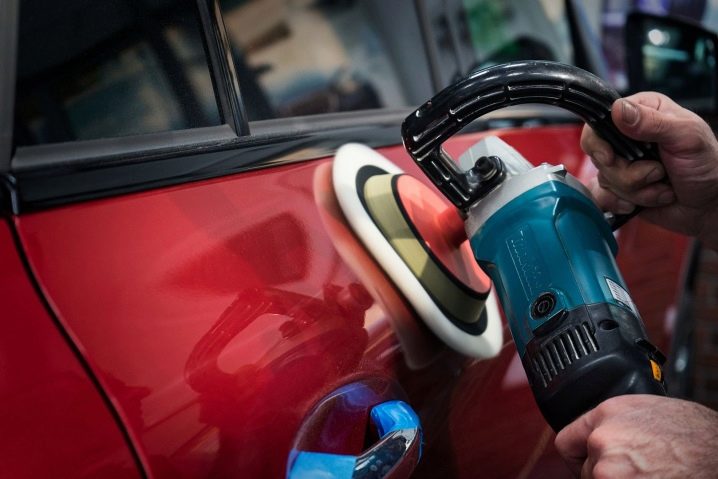
Subtelności wyboru
Aby wybrać odpowiednią maszynę do polerowania, należy przede wszystkim zwrócić uwagę na moc. Ta liczba może wahać się od 0,8 do 2,5 kW. Należy również wziąć pod uwagę tempo, w jakim tarcza się kręci. Maksymalna wartość to 10 tysięcy obrotów na minutę.
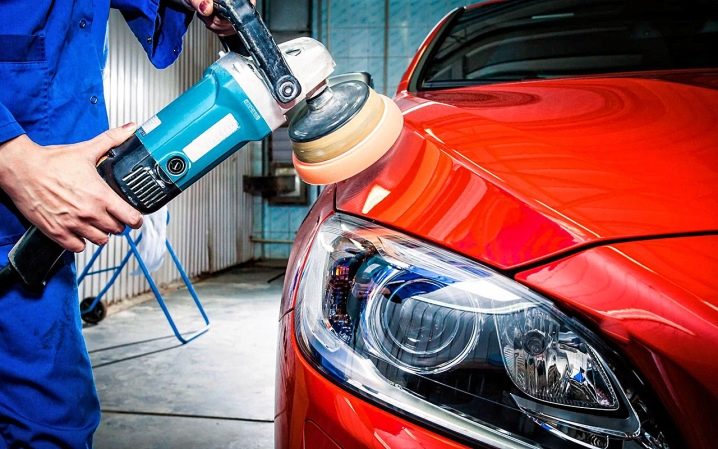
Ważne: należy kupować tylko maszyny do polerowania z regulatorem prędkości. Dzięki temu zapewniony jest wybór trybu pracy zgodnie z cechami nawierzchni.
Zaleca się, aby niedoświadczeni i niedoświadczeni użytkownicy preferowali maszyny z automatyczną regulacją. Takie narzędzie pozwala polerować wszystko bez obawy o uszkodzenie. Ale nadal warto ćwiczyć na starych, oczywiście niepotrzebnych częściach i powierzchniach. Systemy zasilane bateryjnie są bardziej mobilne niż systemy typu plug-in.
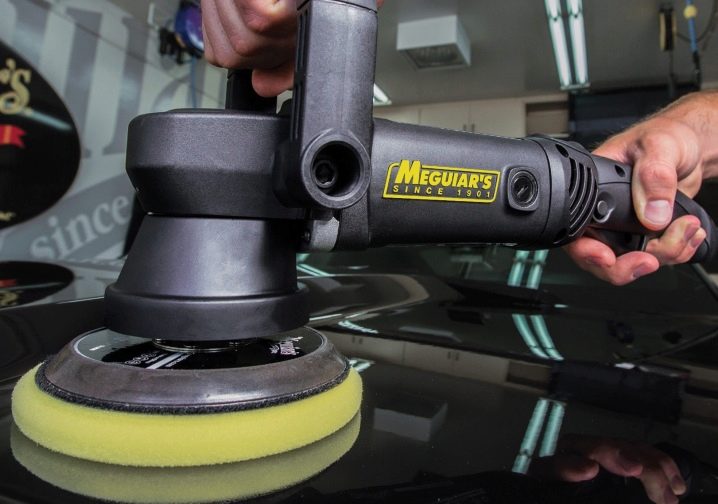
Poniższy film pomoże Ci wybrać odpowiednią maszynę do polerowania.
Wyświetlenia
W zależności od rodzaju napędu zwyczajowo rozróżnia się maszyny do polerowania pneumatycznego i elektrycznego. Zaletą konstrukcji pneumatycznej jest to, że napęd sprężarki nie wymaga zużycia energii. Ponadto takie urządzenie jest najbardziej stabilne i nie nakłada specjalnych wymagań podczas pracy. Urządzenia elektryczne mają jednak ważną zaletę – zwiększoną mobilność (ze względu na brak wiązania z przewodami doprowadzającymi powietrze). Wymienne akumulatory umożliwiają korzystanie z urządzenia nawet tam, gdzie nie ma stabilnego zasilania.
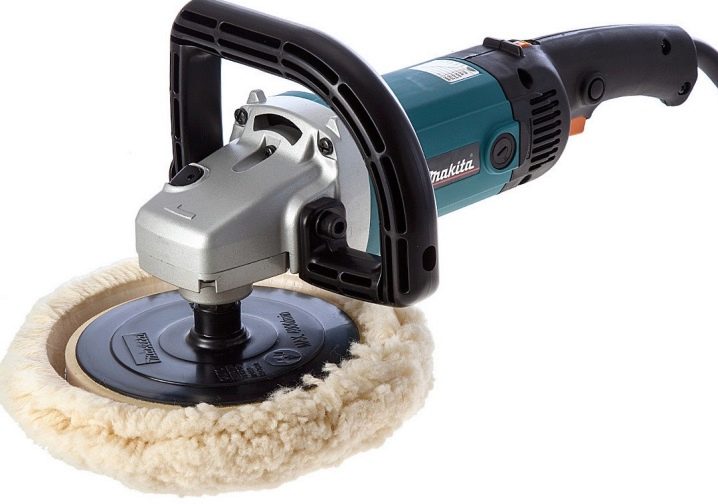
Na uwagę zasługują ekscentryczne (orbitalne) maszyny do polerowania – eksperci uważają takie urządzenia za najbardziej wydajne. Bardzo ważna jest również umiejętność pracy z różnymi powierzchniami. System szlifowania i polerowania orbitalnego jest wyposażony w okrągłą platformę. Części szlifierskie są zamocowane na tej „płycie nośnej”. Płyty robocze wykonane są z:
- runo;
- gąbki;
- poczuł;
- korund;
- futra i inne surowce.
Do mocowania klocka szlifierskiego można użyć zarówno rzepu, jak i klipsa. Pierwsza metoda jest doceniana za wygodę, a druga - za ekonomię. Warto pamiętać, że maszyny mimośrodowe generują znaczną ilość pyłu. Dlatego niektórzy producenci wyposażają swoje produkty w kanały, przez które zostanie przekierowana. Główną funkcją podeszwy jest dokładne szlifowanie (wytwarzane przez ruchy obrotowe), a pomocnicza obróbka w przód i w tył pomaga poprawić wynik.
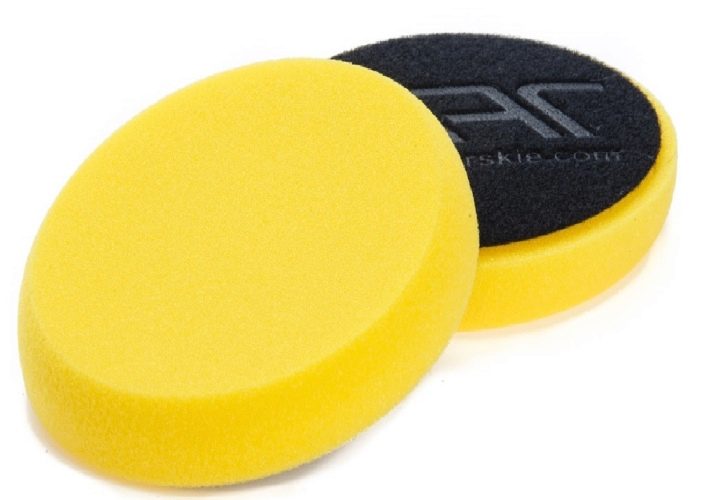
Szlifierka mimośrodowa jest dostępna w różnych poziomach mocy, od 150W do 1000W. W przypadku najprostszych manipulacji możesz ograniczyć się do urządzeń o małej mocy - nie więcej niż 400 watów. Intensywniejsza praca silnika jest potrzebna tylko do zgrubnego szlifowania twardych materiałów. Niektóre urządzenia są w stanie dostarczyć ponad 2000 W mocy, jednak modele te mogą pracować tylko w trybie „mokrym”.
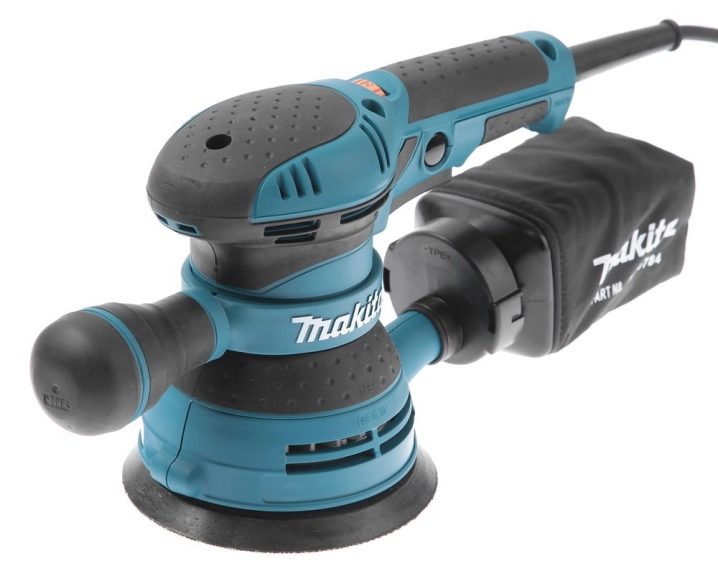
W większości przypadków polerki mimośrodowe są wyposażone w tarcze 125 mm. To rozwiązanie wyróżnia się najbardziej racjonalną amplitudą drgań podczas wykańczania. Jednak najpoważniejsze prace są z powodzeniem wykonywane tylko z urządzeniami, które pozwalają na użycie kół o średnicy do 215 mm.
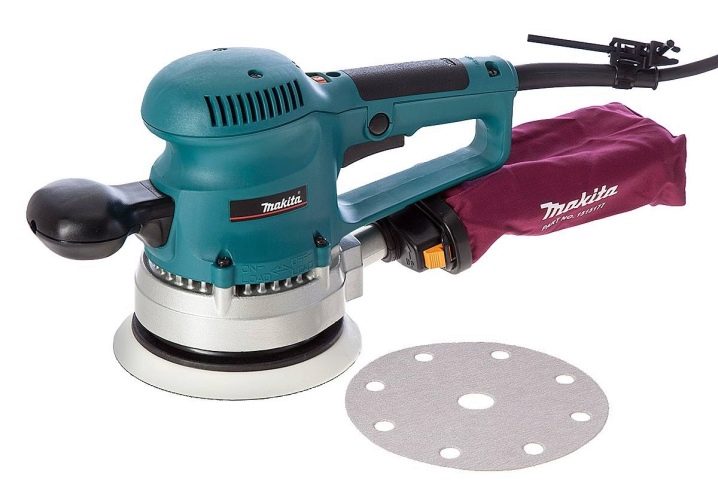
Mimośrodowe systemy polerskie charakteryzują się szerokim zakresem zastosowań. Działają równie wydajnie jak kompleksy wibracyjne. Pod względem mocy orbitalna maszyna do polerowania jest porównywalna z mechanizmami pasowymi. Co ważne, może również szlifować obrabiane powierzchnie. Wybierając urządzenia ekscentryczne, nie należy zapominać o różnicy między modelami domowymi a profesjonalnymi.
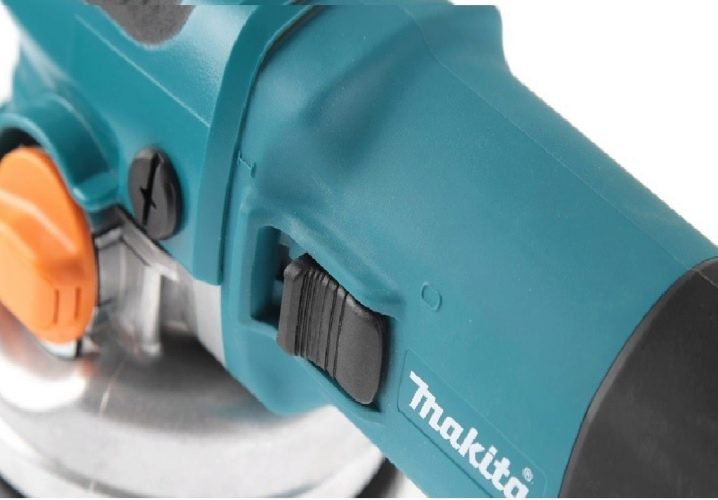
Wersje używane w domu służą głównie do polerowania drewna. Z reguły są to systemy o stosunkowo małej mocy, zdolne do pracy tylko z częstymi przerwami. Jeśli wiadomo, że będziesz musiał obrabiać metal i kamień, powinieneś preferować wersje profesjonalne. Te ekscentryczne polerki są bardzo ciężkie. Ale mogą działać przez bardzo długi czas, jednocześnie stabilnie oszczędzając zasoby robocze.
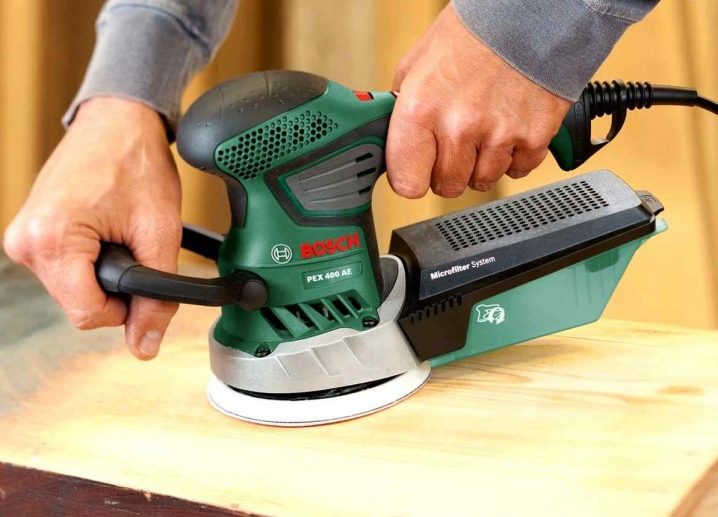
Szlifierka do podłóg i polerka mogą wydajnie obrabiać beton i kamień naturalny.
Wysokiej jakości urządzenia tego formatu są w stanie:
- wyrównaj podstawę;
- przygotować go do wykończenia;
- przeszlifować powierzchnię do idealnego stanu;
- do zagęszczenia i utwardzenia obrabianej warstwy.
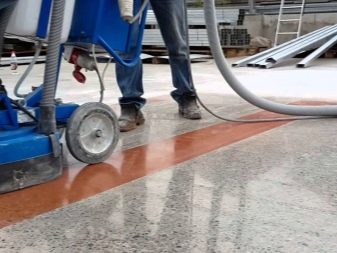
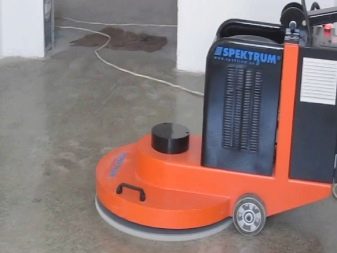
Uwaga: polerowanie podłóg staje się skuteczne dopiero po uzupełnieniu urządzenia o odkurzacz przemysłowy. W przeciwnym razie wszystko wokół będzie bardzo mocno pokryte kurzem.
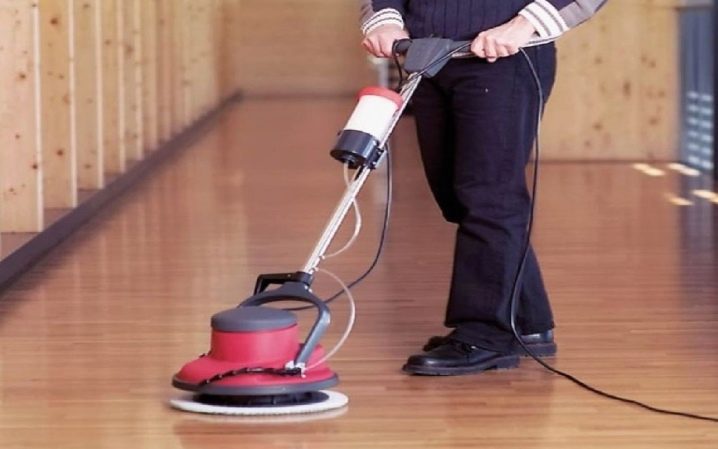
Przygotowując się do szlifowania podłogi, należy wziąć pod uwagę wielkość ziarna i wytrzymałość mechaniczną narzędzia diamentowego. Podczas szlifowania duże znaczenie ma zwiększony nacisk na obrabianą powierzchnię. Dlatego bardziej wartościową opcją okazują się auta, które można obciążyć dodatkowymi ładunkami.
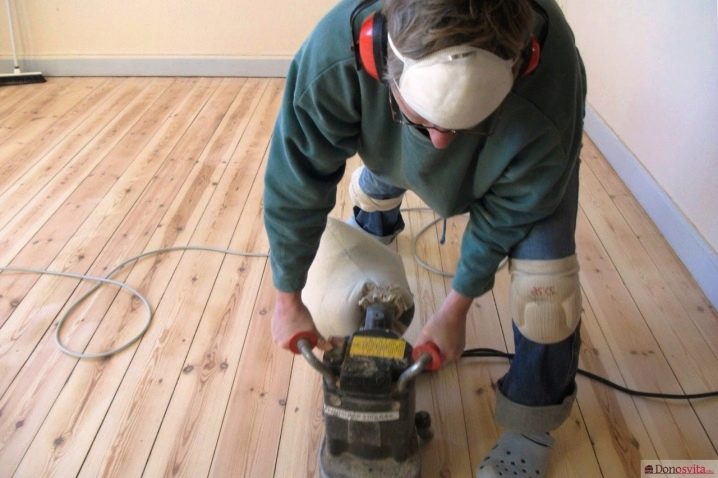
Wysokiej jakości szlifierki i polerki (m.in. marki Hodman) wyposażone są w przekładnie planetarne i silniki o dużej mocy. Dobre mechanizmy wykorzystują chromowane stalowe uchwyty narzędziowe. Uchwyty te muszą być zamocowane, aby ruch odbywał się płynnie i szybko, nawet na nierównych powierzchniach. Ten stan znacznie zwiększa sterowność maszyny.
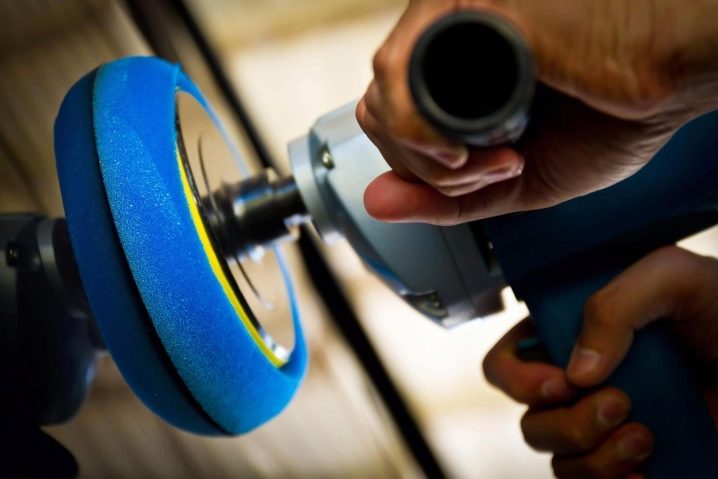
Do polerowania samochodów stosowane są ręczne mechanizmy obrotowe. Wraz z nimi można stosować systemy orbitalne. Różnica między nimi to liczba osi obrotu (odpowiednio 1 i 2). Linie wiodących firm obejmują zarówno modele obrotowe, jak i okrągłe. Każda odmiana nadaje się do określonego zadania.
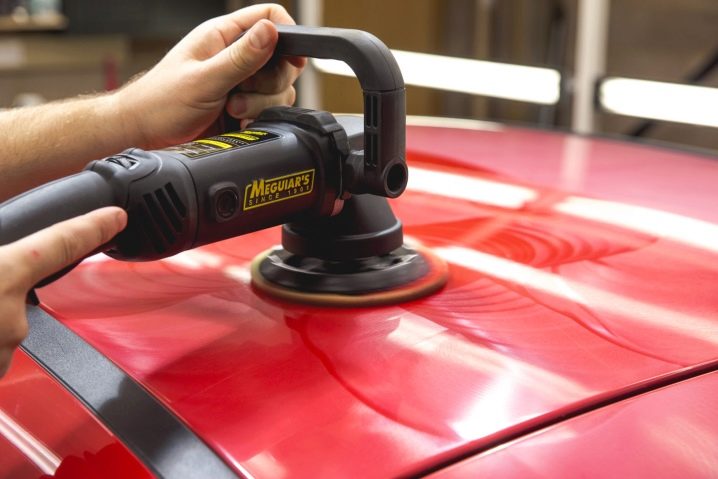
Aparat rotacyjny jest lepszy niż orbitalny:
- według poziomu wydajności;
- przez różne średnice podłoża;
- na zwrotność części roboczej;
- uratować wysiłki budowniczego;
- według poziomu hałasu;
- wspólne bezpieczeństwo;
- przez czas trwania operacji.
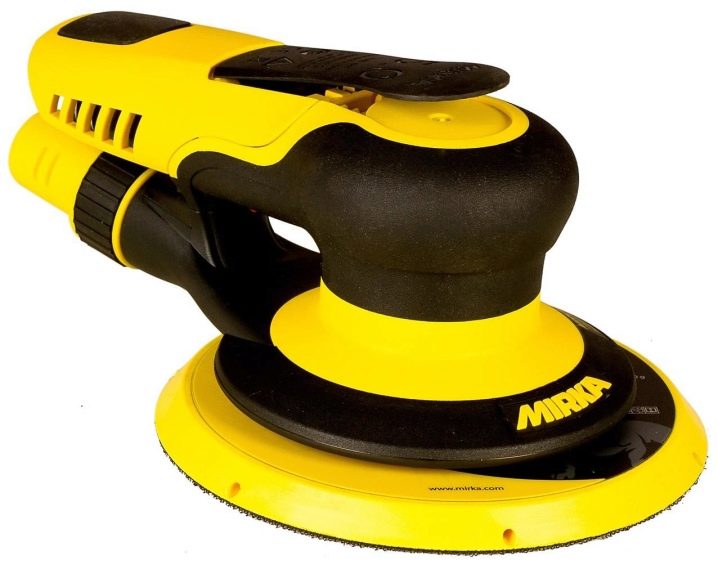
Należy pamiętać, że systemy wirników mają raczej niską wydajność.Dlatego generują mniej ciepła. Zmniejsza się również ryzyko uszkodzenia lakieru. Pojawienie się defektów „holograficznych” jest prawie wykluczone. Takie narzędzie świetnie nadaje się do miękkiego polerowania, jednak nie pomaga w polerowaniu twardych lakierów.
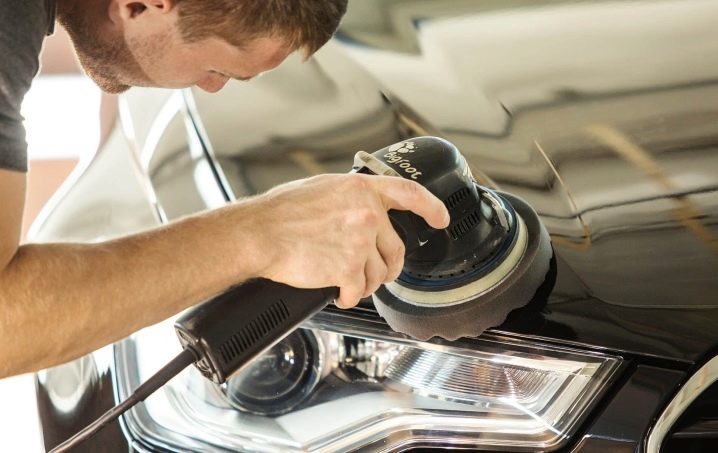
Biorąc pod uwagę znaczenie polerowania samochodu, należy powiedzieć jeszcze kilka słów o maszynach do obróbki drewna. Takie urządzenia mają różne obszary zastosowań. Niektóre opcje pomagają wygładzić nierówności, podczas gdy inne służą do wykończenia.
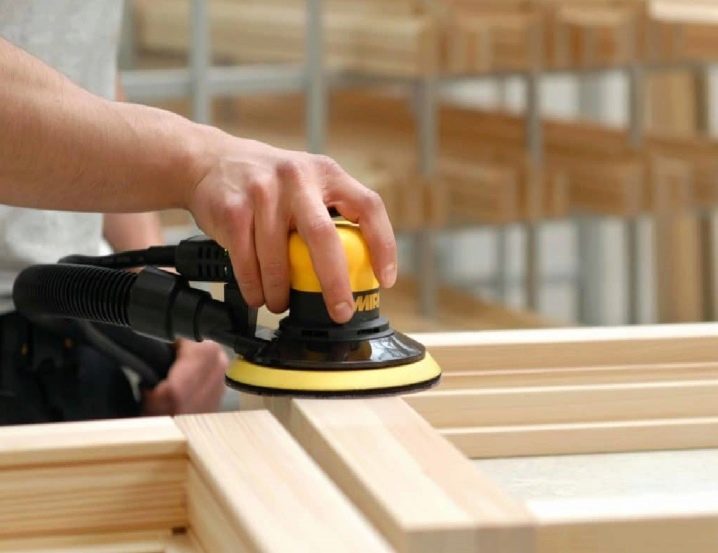
Ważne: Nie próbuj używać szlifierek kątowych i maszyn taśmowych do szlifowania drewna. Wtedy powierzchnia będzie zbyt szorstka.
Drewno obrabiane jest maszynami mimośrodowymi. Mimo swojej lekkości i braku specjalnego hałasu, doskonale pomagają w obróbce zakrzywionych powierzchni, a także powierzchni profilowanych. Narożniki krążków można łatwo wciągnąć we wgłębienia i nacięcia. Jednocześnie jednak narzędzie może w krótkim czasie przetworzyć duży blok drewna.
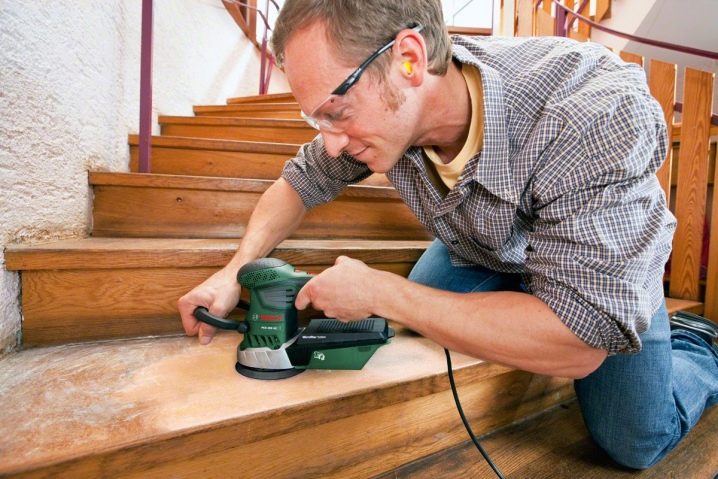
Czasami drewno jest polerowane i szlifowane za pomocą systemów wibracyjnych. Wyposażone są w podeszwy trójkątne lub prostokątne. W wykańczaniu pomagają mechanizmy wibracyjne. Jednak wydajność takich urządzeń jest nadmiernie niska. Ponadto maszyna wibracyjna, nawet trójkątna, nie może pracować w pobliżu ściany lub innej przeszkody.
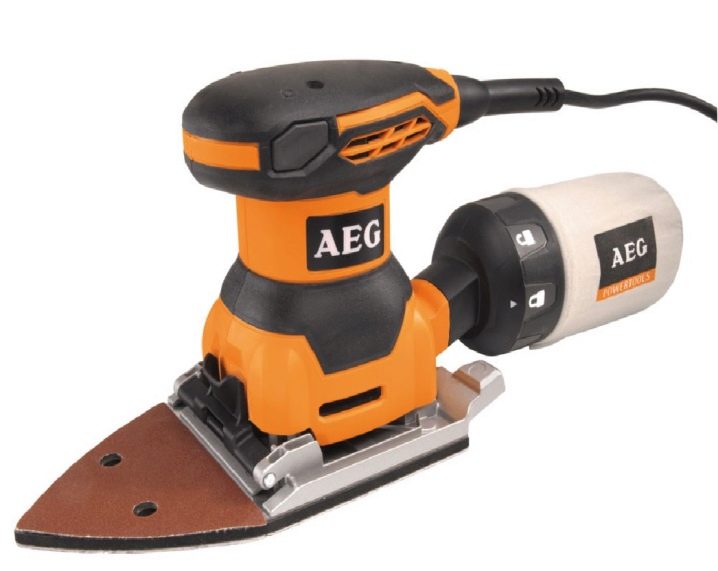
Narzędzie do polerowania i szlifowania kamienia niezmiennie posiada części robocze z cząstkami diamentowymi. Do pełnego przetworzenia wymagany jest cały zestaw krążków z ziarnami różnych frakcji. Wybierając narzędzia, zwróć uwagę na:
- kolor przetworzonego kamienia;
- zasób części roboczej;
- ilość pracy;
- skuteczność, regularność i intensywność manipulacji.
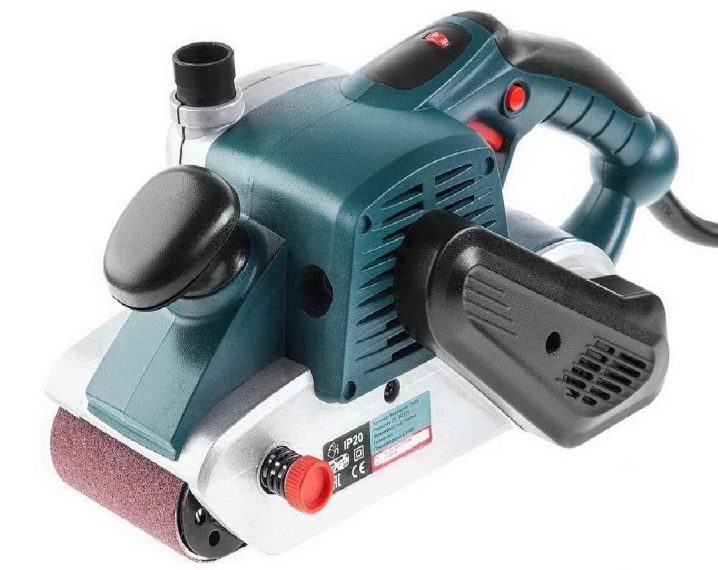
Do pracy na betonie narzędzia przeznaczone do manipulowania kamieniem naturalnym nie są odpowiednie. Specjalistyczne mocowania mogą nadać powierzchni betonu idealną gładkość i zwiększyć jej wytrzymałość. Jednocześnie zmniejsza się przepuszczalność materiału na wodę. Pomimo wszystkich różnic między poszczególnymi modelami, projekty są dość zbliżone. Obrotowy zespół jest uzupełniony elementem ściernym zdolnym do usunięcia wierzchniej warstwy sztucznego kamienia.
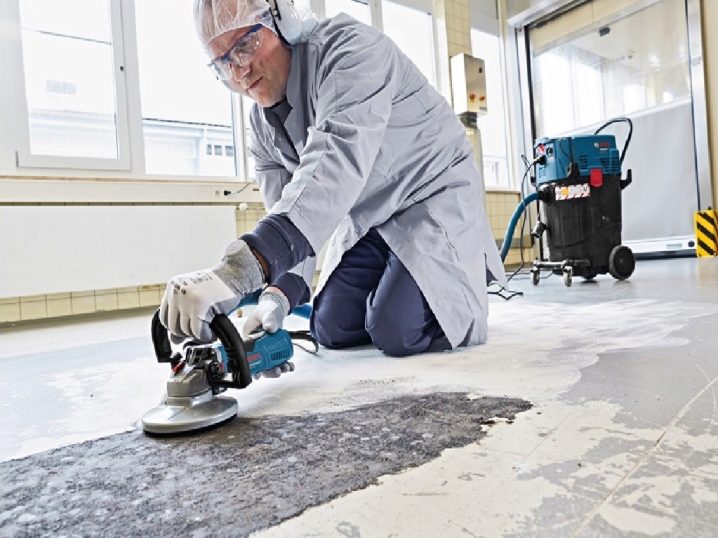
Za pomocą polerek i szlifierek możesz:
- wygładzić świeży jastrych betonowy;
- wygładzić masę do wykończenia;
- usunąć popękaną, szybko gnijącą warstwę;
- pozbyć się drobnych deformacji;
- zwiększyć przyczepność do późniejszego powlekania farbami i lakierami.
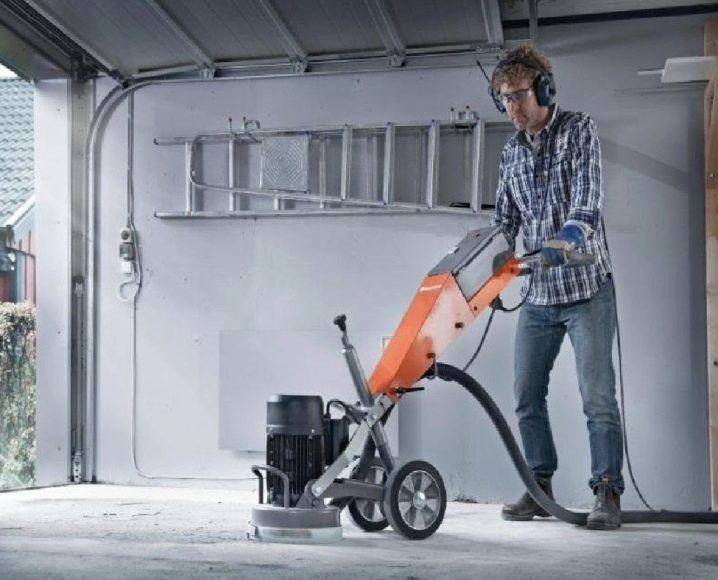
Ocena najlepszych modeli
Podsumowując przegląd odmian technologii polerowania i szlifowania możemy śmiało stwierdzić, że są one bardzo różnorodne. Istnieje jednak kilka modeli, które zasługują na szczególną uwagę. Wśród niedrogich wersji, o których warto wspomnieć Sturm AG1014P... To urządzenie, choć sygnowane logo niemieckiej marki, jest montowane w Chinach. Projektantom udało się stworzyć doskonały mechanizm zdolny do usuwania brudu i niepotrzebnej powłoki, a także sztucznego starzenia drewna.
Silnik elektryczny o mocy 1400 W obraca się z prędkością do 3000 obrotów na minutę. Całkowita waga narzędzia to tylko 3,35 kg. Dostępne są opcje miękkiego startu i zatrzaskiwanie klawisza wyzwalacza. Prędkość obrotowa w trybie obciążonym utrzymywana jest na stabilnym poziomie. Bardziej zaawansowaną (profesjonalną) opcją jest Bosch GSI 14 CE.
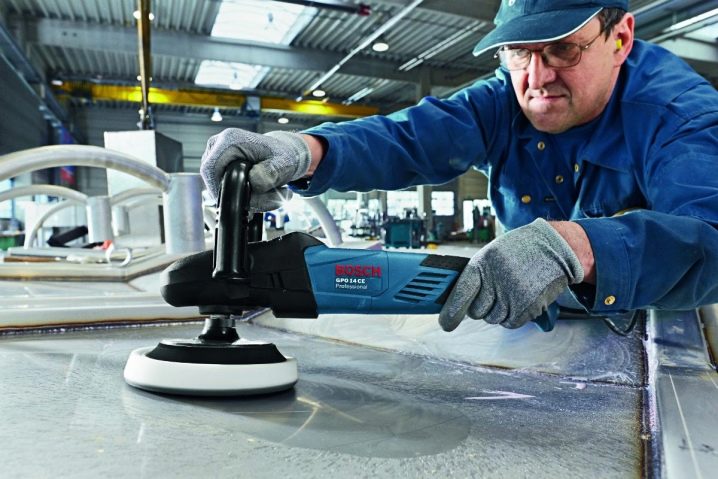
Podobny model maszyny do polerowania jest zdolny do obróbki zgrubnej i dekoracyjnej na wysokim poziomie szerokiej gamy materiałów. Silnik elektryczny, podobnie jak w poprzedniej wersji, ma moc 1400 W, a prędkość obrotowa wału jest taka sama. Uchwyty maszyny są gumowane. Całkowita waga to 3,5 kg. Sądząc po recenzjach, takie narzędzie jest dość wygodne i bezpieczne w użyciu. Ale tego modelu nie można w żaden sposób nazwać budżetem.
Trzeba będzie zapłacić znaczną sumę pieniędzy Makita BO6040... Za pomocą tego urządzenia można usunąć rdzę i polerować różne płaskie powierzchnie. BO6040 jest uważany za idealny do lakierowania samochodów. Wyznaczenie liczby drgań i prędkości obrotowej wału odbywa się za pomocą układu elektronicznego. Dzięki płynnemu rozruchowi obróbka odbywa się w sposób delikatny.
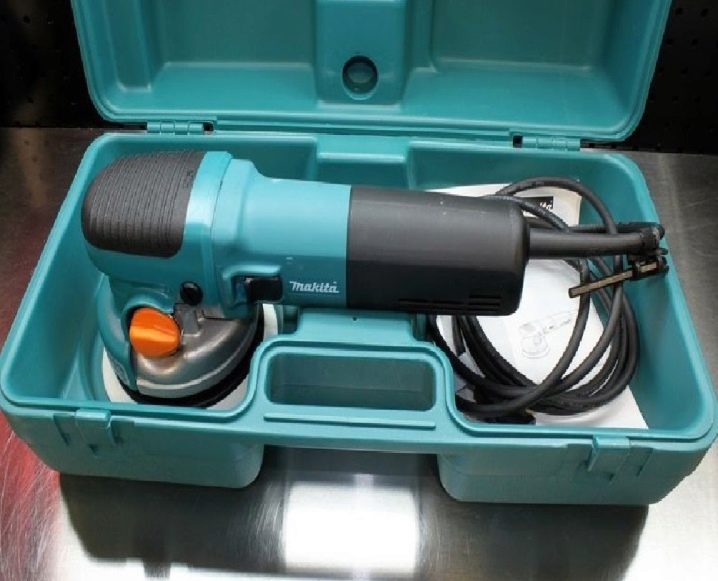
Oprawy i części zamienne
Niezależnie od konkretnego modelu polerki ważną rolę odgrywa jej wyposażenie pomocnicze. Wśród dysz torba wyróżnia się swoją rolą. Pozwala zebrać jak najwięcej gruzu, kurzu i odpadów. Dzięki temu praca jest wykonywana tak czysto, jak to możliwe.
Samoprzylepne podkładki podporowe umożliwiają przymocowanie tarcz szlifierskich do uchwytów. Specjalne elastyczne wałki ułatwiają pracę w trudno dostępnych miejscach. Do samego szlifowania stosuje się szczotki lub wałki wykonane z nylonu, metalu i specjalnych kompozytów. Polerki dostarczane są z rękojeścią główną i pomocniczą. Ale przy wyborze takich komponentów należy dokładnie sprawdzić, aby ułatwiały pracę i nie komplikowały jej.
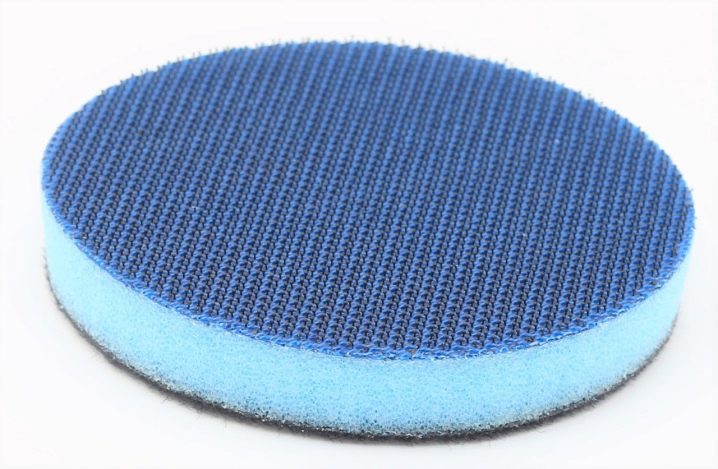
Podeszwa do maszyny wibracyjnej, jak już wspomniano, może być wykonana w formie trójkąta lub prostokąta. Pierwszy typ przejawia się lepiej w ograniczonej przestrzeni, drugi - w przypadkach, gdy konieczne jest przetworzenie maksymalnej powierzchni. Jeśli początkowy przewód zasilający jest krótki, będziesz musiał używać przedłużacza w sposób ciągły. Oczywiście wszystkie części zamienne i elementy pomocnicze należy kupować tylko od oficjalnych producentów.
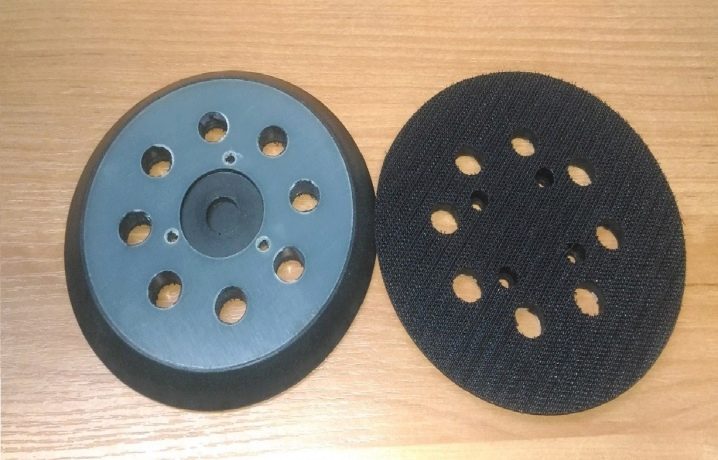
Wskazówki dotyczące użytkowania
Możesz użyć polerki do obróbki karoserii tylko po nałożeniu specjalnej pasty na powierzchnię. Pod względem składu chemicznego lek ten jest dość złożony. Przygotowując się do pracy, musisz przygotować kilka tarcz polerskich: jedną do szorstkości, a drugą do subtelnych efektów. Na dyski nakłada się niewielką ilość pasty. Dlatego niemożliwe jest przetwarzanie dużych powierzchni w jednym kroku.
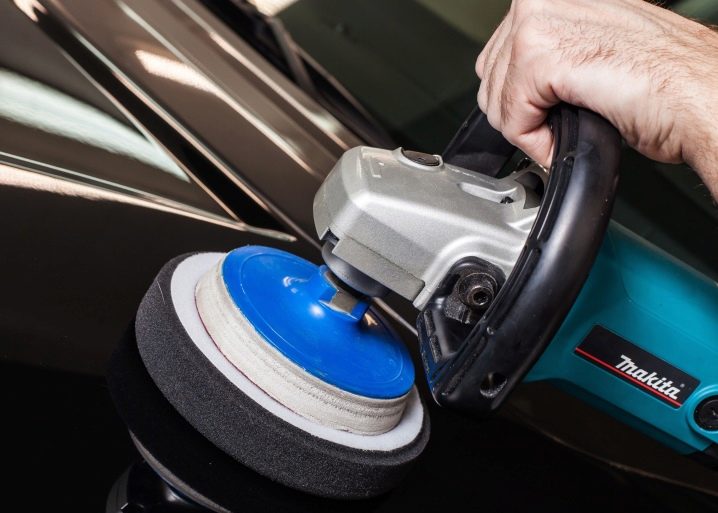
Szybkość obróbki zgrubnej powinna być minimalna, a gdy praca zbliża się do logicznego końca, wzrasta. Równomierne rozprowadzenie pasty uzyskuje się, gdy prace wykonuje się metodą „na krzyż” – początkowo poziomo, a następnie pionowo. Podejście do polerowania drewna powinno być inne. Aby uzyskać dobry wynik, należy dokładnie przestudiować cechy konkretnej maszyny i zalecenia producenta. Należy również wziąć pod uwagę cechy konkretnego gatunku drewna.
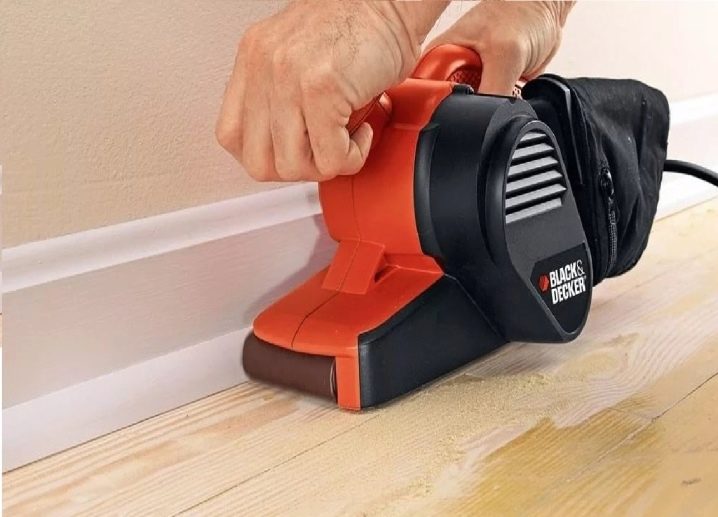
Komentarz został wysłany pomyślnie.