Pale żelbetowe: specyfikacje i zalecenia montażowe
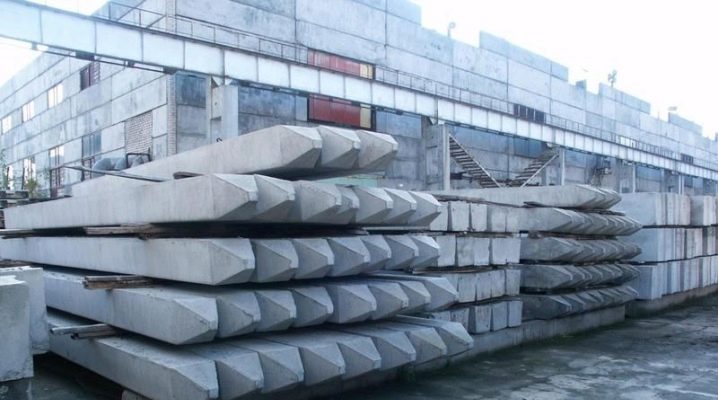
Pale żelbetowe to najbardziej poszukiwany rodzaj podpór do organizacji posadowienia palowego. Wynika to z ich trwałości, wysokiej nośności, odporności na wilgoć oraz możliwości montażu przy użyciu kilku technologii.
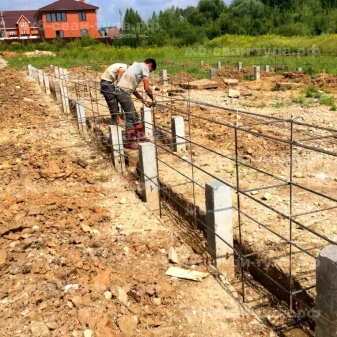
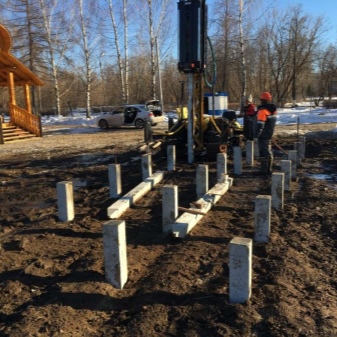
Osobliwości
Pale żelbetowe (RC) to klatka wzmacniająca wylewana zaprawą betonową. Długość gotowego produktu może wynosić od 3 do 12 m.
Pale żelbetowe stosuje się przy organizowaniu fundamentów za pomocą technologii wbijania. Ich zastosowanie pozwala na wzmocnienie podłoża i dotarcie do warstw gruntu stałego.
Wizualnie reprezentują podstawy o okrągłym (pustym lub wypełnionym), kwadratowym przekroju. Różnią się średnicą i wysokością, co decyduje o nośności i zakresie zastosowania. Ponadto wskaźniki wytrzymałości zależą od użytego gatunku betonu. Im jest wyższy, tym bardziej niezawodne są elementy.
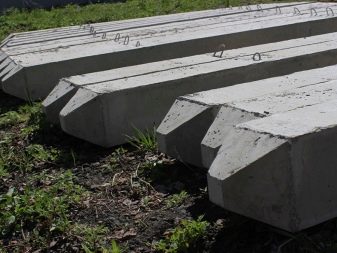
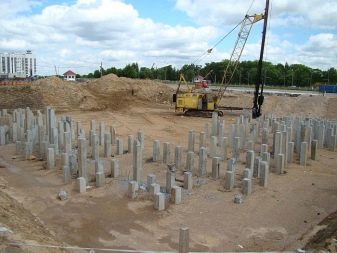
Do tworzenia pali żelbetowych stosuje się cement, którego wytrzymałość marki jest nie mniejsza niż M100. Nie tylko wytrzymałość pala na ściskanie zależy od właściwości użytkowych betonu, ale także mrozoodporności i odporności na wilgoć. Ostatnie parametry dla gatunku betonu M100 to F 50 (czyli konstrukcja może wytrzymać do 50 cykli zamrażania / rozmrażania) i W2 (ciśnienie słupa wody) - 2 MPa. Ciężar podpory zależy od jego wymiarów, a także od gęstości użytego rodzaju betonu.
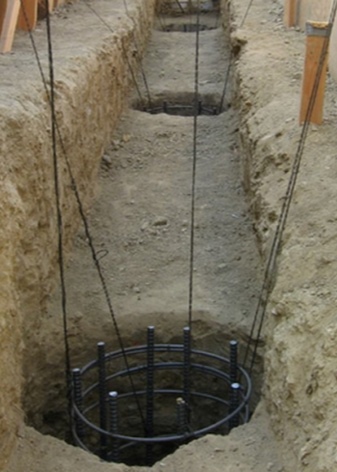
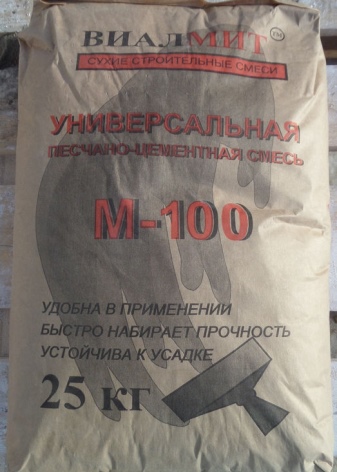
Zwykle stosuje się bardziej gęste gatunki betonu M-250, M-300, M-400. Mrozoodporność takich produktów sięga 150 cykli, a współczynnik wodoodporności wynosi co najmniej 6.
Ze względu na zwiększoną odporność na możliwość wbijania pali na duże głębokości, ich zastosowanie staje się możliwe na gruntach ruchomych (w tym w strefie wzmożonej aktywności sejsmicznej), na glebach gliniastych, falujących i słabych, na gruntach nasyconych wodą i bagiennych.
Pale żelbetowe mogą być stosowane nie tylko jako fundament fundamentu, ale również stosowane do zapobiegania kruszeniu się wykopu, wzmacniania gruntu i istniejącego fundamentu palowego. W tym celu podpory żelbetowe są zanurzone w niewielkiej odległości od istniejących konstrukcji, pełniąc funkcję drugiego pala. Ponadto, przy dodatkowym wzmocnieniu fundamentu, rozważany rodzaj podparcia można przeprowadzić poza istniejący fundament i połączyć z nim za pomocą belek.
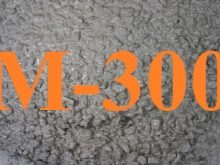
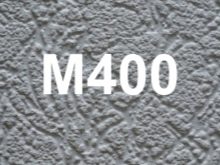
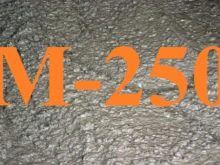
Zalety i wady
Wśród zalet podpór żelbetowych zwykle wyróżnia się kilka cech.
- Długi okres eksploatacji - do 100 lat, w zależności od technologii montażu. Informacje zwrotne od właścicieli sugerują, że taki fundament może trwać do 110-120 lat bez konieczności poważnych napraw.
- Wskaźniki wysokiej wytrzymałości - średnio jedna podpora może wytrzymać od 10 do 60 ton. Ze względu na tę cechę ten rodzaj pala stosuje się do budowy obiektów przemysłowych, wielokondygnacyjnych budynków mieszkalnych oraz konstrukcji wykonanych z ciężkich płyt.
- Stabilność strukturalna na wszystkich rodzajach gruntu, co osiąga się dzięki znacznemu pogłębieniu pala betonowego. To z kolei umożliwia oparcie elementów betonowych na głębokich warstwach gruntu o maksymalnej nośności.
- Możliwość prowadzenia budowy na gruntach ruchomych, reliefowych, przy użyciu stosów o różnej długości.
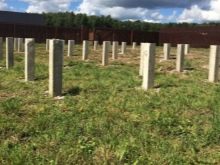
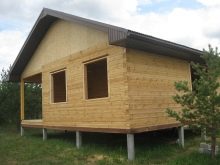
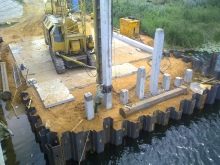
Wadą jest znaczna masa konstrukcji, która komplikuje proces transportu i montażu elementów.
Wymogi regulacyjne
Produkcja jest regulowana przez TU (warunki techniczne), których główne punkty są regulowane zgodnie z GOST 19804, przyjętą w 1991 roku. Żywotność produktów wynosi 90 lat.
Produkty żelbetowe zgodne z określonym GOST są stosowane w budownictwie jedno- i wielokondygnacyjnym z różnych materiałów, w budowie obiektów transportowych, inżynieryjnych, mostowych, obiektów rolniczych i przemysłowych oraz konstrukcji hydraulicznych.
Jednym słowem, we wszystkich tych obiektach, od których podstaw wymagana jest zwiększona wytrzymałość, zachowanie właściwości użytkowych nawet w warunkach stałej wilgotności i pod wpływem środowisk korozyjnych.
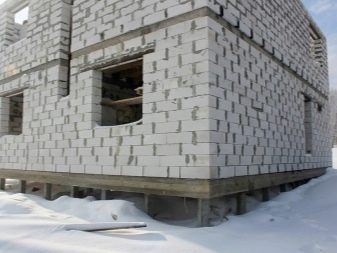
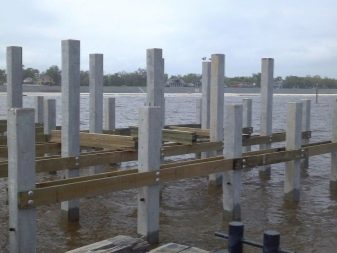
GOST 19804-2012 to dokument normatywny regulujący cechy produkcji pali żelbetowych wbijanych fabrycznie. Jeśli mówimy o zbrojeniu, zastosowana stal musi spełniać wymagania GOST 6727.80 i 7348.81 (wymagania dotyczące drutu opartego na stali węglowej i niskowęglowej stosowanej jako zbrojenie).
Budowa obiektów mostowych wiąże się z własnymi przepisami. Zastosowane podpory muszą być zgodne z GOST 19804-91. Do ich produkcji stosuje się beton o wytrzymałości M350, sama konstrukcja jest wzmocniona zbrojeniem podłużnym. Tylko takie elementy zapewnią wytrzymałość i niezawodność całej konstrukcji przyszłego mostu.
Te same monolityczne pale są wykorzystywane do budowy wieżowców wielopiętrowych, wielkogabarytowych obiektów przemysłowych. Kolejność selekcji, sposób zakopywania, kontrola jakości i specyfika badań pali wbijanych znajdują odzwierciedlenie w SNiP 2.02.03 -85.
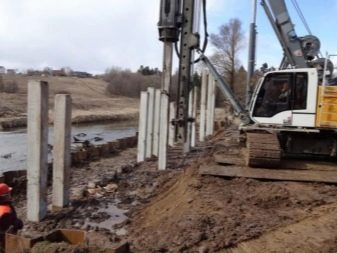
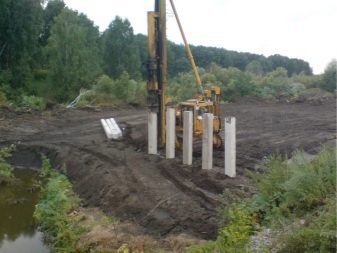
Wyświetlenia
Klasyfikację podpór tego typu można przeprowadzić na podstawie kilku kryteriów. Ogólnie wszystkie pale żelbetowe są podzielone na 2 rodzaje - ramy, wylewane betonem bezpośrednio na placu budowy i analogi, produkowane w fabryce.
Rodzaj pali w pewien sposób zależy od ich urządzenia - technologii instalacji. Tak więc pale, które są wsypywane bezpośrednio po wbiciu w grunt, można montować poprzez wbijanie młotami hydraulicznymi, za pomocą wibracyjnego pogłębienia lub w technologii wgniatania pod wpływem statycznego (stałego) nacisku.
Jeśli mówimy o gotowych konstrukcjach, stosuje się jedną z następujących metod instalacji - iniekcję gruntowo-cementową, wierconą lub wierconą.
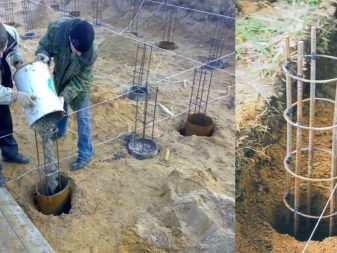
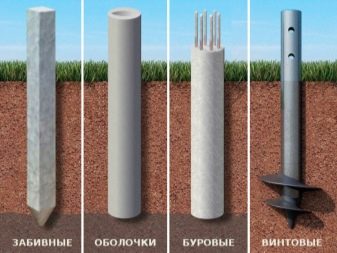
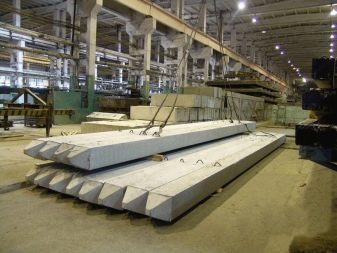

W zależności od cech konstrukcyjnych pale żelbetowe dzielą się na kilka typów.
Monolityczny
Stanowią solidną podporę o przekroju prostokątnym lub kwadratowym, chociaż możliwe są pale o przekroju okrągłym, trapezowym lub teowym, których wielkość wynosi 20-40 mm. Dolny koniec ma kształt gruszki, może być ostry lub tępy. Takie podpory nie są puste, więc nie trzeba robić otworów, aby zanurzyć je w ziemi. Wykorzystywana jest technologia wbijania młotków lub wibracji w glebę. Są szeroko stosowane w inżynierii lądowej, są również poszukiwane przy budowie domu prywatnego (drewnianego, blokowego, szkieletowego).
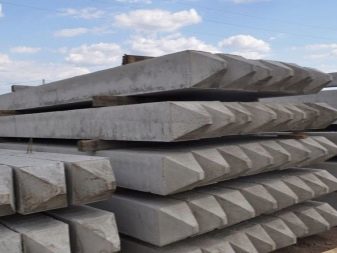
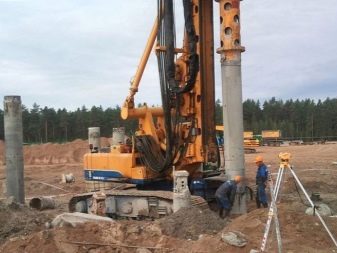
Pusta muszla)
Wygląda jak muszla, do zanurzenia w glebie, której studnia jest wstępnie przygotowana. Podpora może być okrągła lub kwadratowa, ale ta ostatnia nadal ma okrągły przekrój. Podpory drążone z kolei dzielą się na lite i kompozytowe (składają się z kilku elementów, które składa się bezpośrednio przed zanurzeniem).
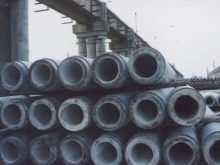
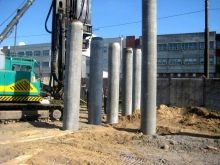
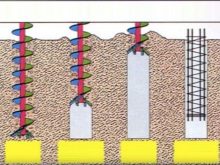
Drukowane
Ale montuje się go również przez zanurzenie we wcześniej przygotowanej wnęce.
W zależności od rodzaju zbrojenia pale żelbetowe są następujących typów:
- podpory ze zbrojeniem podłużnym nienaprężonym ze zbrojeniem poprzecznym;
- Podpory ze sprężonym zbrojeniem podłużnym ze zbrojeniem poprzecznym lub bez.
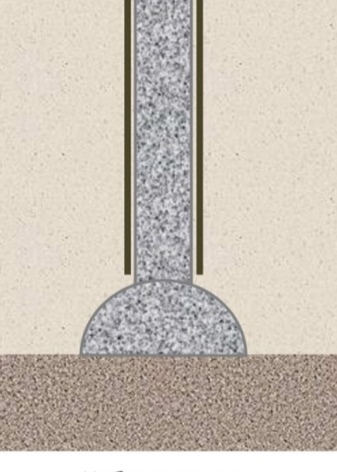
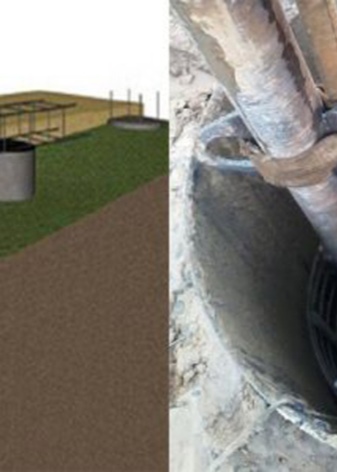
Jeśli mówimy o kształcie przekroju stosów, to są one okrągłe (puste lub pełne), kwadratowe, kwadratowe z okrągłym wgłębieniem, prostokątne. Niedopuszczalne jest umieszczanie podpór o przekroju kwadratowym w wiecznej zmarzlinie. Nawet przy lekkim rozmrożeniu stos potoczy się, a budynek się przekrzywi. W rejonach o zwiększonej aktywności sejsmicznej należy stosować konstrukcje o przekroju kołowym.
Przydziel konstrukcje jednoczęściowe i prefabrykowane. Drugie składają się z kilku segmentów, co umożliwia zwiększenie wysokości produktu. Segmenty są mocowane przez spawanie lub za pomocą połączenia śrubowego.
Wytrzymałość i dodatkowa niezawodność połączenia segmentów zapewnia obecność złącza typu „szkło” na każdym kolejnym segmencie.
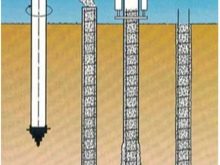
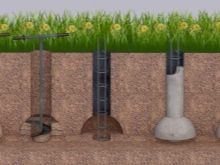
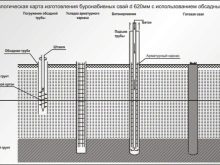
Montowanie
Montaż pali poprzedzają badania geologiczne i pobieranie próbek gruntu o różnych porach roku. Na podstawie wyników uzyskanych podczas analizy podejmowana jest decyzja o metodach wbijania pali. Opracowywana jest również dokumentacja projektowa, w której m.in. obliczane jest obciążenie łożyska dla jednego elementu pala, określa się ich wielkość i liczbę.
Kosztorys obejmuje nie tylko koszt zakupu pali, ale także ich transport na plac budowy, przyciągnięcie (zakup lub wynajem) specjalnego sprzętu.
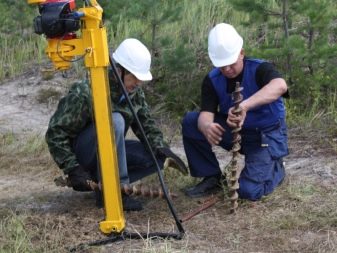
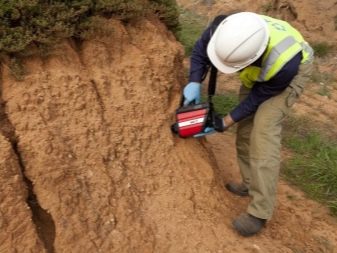
Następnym krokiem jest próbna jazda podpory, która pozwala ocenić, jak podpora zachowuje się w praktyce. Po przejechaniu zostaje na jakiś czas (od 3 do 7 dni), podczas którego prowadzone są również obserwacje.
Do wbijania pali przykładane są siły dynamiczne i statyczne - uderzenia w powierzchnię nośną przykładane są specjalnym młotkiem. Aby zapobiec zniszczeniu i deformacji elementów w tym momencie, pozwalają na to opaski, które chronią głowę podstawy podczas uderzenia.
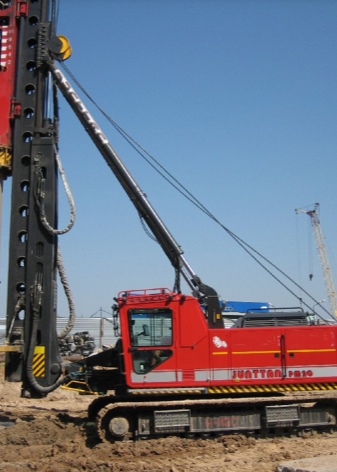
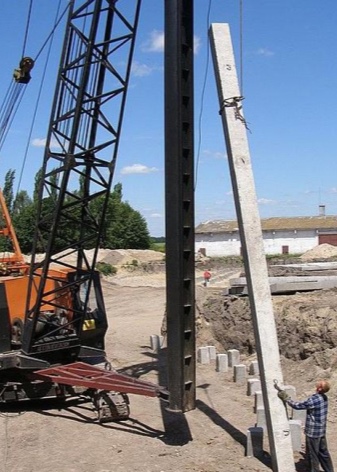
Jeżeli instalacja ma być prowadzona na gruntach nasyconych wodą, lepiej zastosować kafar wibracyjny. Proces montażu polega na sekwencyjnym podnoszeniu, a następnie opuszczaniu pala do gruntu. Cykle te są powtarzane, aż podstawa elementu osiągnie głębokość projektową.
Jeżeli instalacja ma znajdować się na bardzo gęstych i twardych gruntach, można połączyć metodę wbijania i wibrowania z erozją gruntu. Aby to zrobić, woda jest pompowana do studni wzdłuż stosu pod ciśnieniem. Zmniejsza tarcie między elementem a glebą, zmiękczając ją.
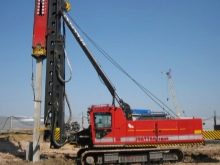
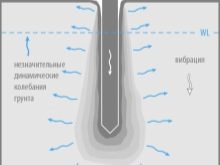
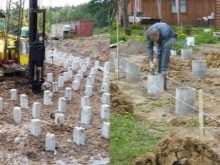
Metoda napędu i wibracji ma zastosowanie do podpór stałych i płaszczowych, ale nie nadaje się do budowy w warunkach miejskich, ponieważ towarzyszy mu silny hałas i wibracje. Te ostatnie mogą negatywnie wpływać na stan fundamentów sąsiednich obiektów.
Pale wklęsłe i wbite są instalowane przy użyciu technologii wiercenia, która zapewnia wstępne przygotowanie kopalni. Wprowadza się do niego podporę, a między jego ściany a boczne powierzchnie kopalni wlewa się podkład lub zaprawę cementowo-piaskową.
Metoda ta charakteryzuje się niskim poziomem hałasu i brakiem drgań podczas zanurzania, nie wymaga angażowania masywnego sprzętu ubijającego ani sprzętu do wytwarzania drgań.
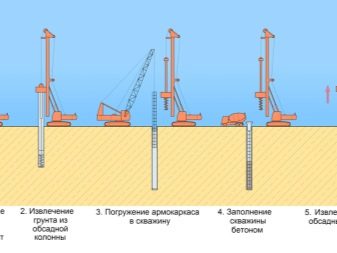
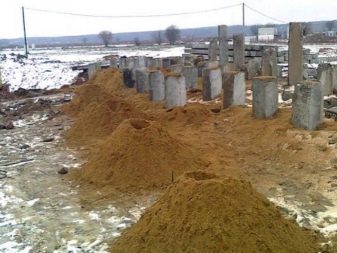
Technologia wiercenia instalacji ma kilka odmian. Tak więc w przypadku gleb gliniastych odpowiednia jest metoda wiercona, w której pusty stos jest opuszczany do studni i betonowany bezpośrednio w ziemi. Ponadto można również zastosować gotowe pale żelbetowe, których mocowanie w studni odbywa się poprzez zasypanie roztworem gliny między bocznymi powierzchniami podstawy a ścianami szybu. Zamiast tego ostatniego można zastosować obudowę.
Metody wiercenia polegają na wstrzyknięciu do studni drobnoziarnistej zaprawy betonowej, natomiast metody wiercenia polegają na wypełnieniu przestrzeni między studnią a umieszczonym w niej stosem zaprawy betonowej.
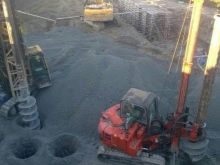
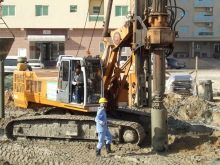
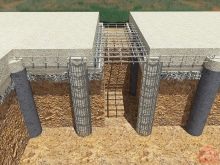
Rada
Pale produkowane są przez duże fabryki lub warsztaty produkcyjne w firmach budowlanych.Z reguły produkty tych pierwszych mają niższy koszt, ale fabryki wolą współpracować z odbiorcami hurtowymi.
Jeśli potrzebujesz ograniczonej liczby podpór, najlepiej skontaktować się z warsztatem renomowanej firmy budowlanej. Z reguły można tu zamawiać stosy co najmniej po sztukach, ale ich koszt będzie wyższy. Wynika to z faktu, że małe firmy nie mogą budować swojej siły, dlatego zwiększają własne przychody poprzez podwyższanie cennika.
Wybór stosów jest lepszy niż produkcja krajowa, ponieważ są one wytwarzane zgodnie z wymaganiami GOST.
Nie ma potrzeby kupowania tanich produktów nieznanych marek, ponieważ od jakości pali zależy wytrzymałość i trwałość fundamentu, a tym samym całego domu.
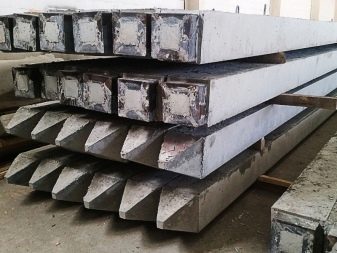
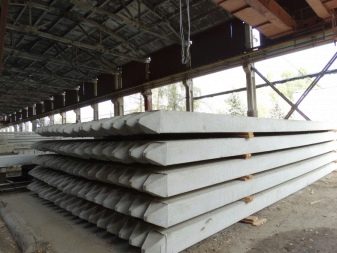
Zwykle cena pala uzależniona jest od jego długości i wymiarów przekroju, a także od klasy wytrzymałości użytego betonu. Najniższy koszt mają trzymetrowe konstrukcje o przekroju kwadratowym, których bok ma 30 cm.
Z reguły im większa partia zakupionych wyrobów betonowych, tym niższy koszt jednej jednostki towaru. Przy rejestracji samodzielnego odbioru w większości przypadków udzielana jest również zniżka.
Więcej o palach żelbetowych dowiesz się z poniższego filmu.
Komentarz został wysłany pomyślnie.