Maszyny ze sklejki wykonujemy własnymi rękami

Wykonywanie krosien ze sklejki własnymi rękami nie jest tak trudne, jak się wydaje. Konieczne jest jedynie przestudiowanie podstawowych rysunków domowych maszyn CNC. Umiejętne podejście pozwala na wykonanie tokarek do drewna własnymi rękami i innymi domowymi produktami o różnych profilach.

Osobliwości
Doświadczeni specjaliści od dawna wiedzą, że domowe CNC do sklejki w niektórych przypadkach nie ustępują pełnoprawnym, fabrycznym metalowym odpowiednikom. Takie konstrukcje stosuje się oczywiście tylko tam, gdzie nie ma znaczących naprężeń mechanicznych, silnych wibracji, nagrzewania i konieczności odprowadzania ciepła wodą. Techniczne właściwości maszyn do sklejki mogą być na przyzwoitym poziomie. Jednocześnie koszt takiej techniki jest oszczędny.
Uwaga: takie systemy są przeznaczone wyłącznie do użytku prywatnego. Maszyna do sklejki nie jest przydatna jako pełnoprawne stanowisko produkcyjne. Zanim to zrobisz, musisz trzeźwo ocenić swoje umiejętności i wiedzę z zakresu sztuki stolarskiej. W przypadku braku specjalnych umiejętności i umiejętności pracy z elektronarzędziami będziesz musiał zapomnieć o samodzielnej produkcji obrabiarek.
Ponadto będziesz musiał starannie wybrać główny materiał konstrukcyjny.



Projekt
Na maszynach, nawet najmniej krytycznych, nie należy zezwalać na arkusze o grubości mniejszej niż 0,6 cm, w każdym razie dotyczy to części nośnych i nośnych zespołu. Czasami wyjątek stanowią obudowy i inne lekkie części. Jednak nawet wtedy konieczne jest dokładne rozważenie zalet i wad, aby prawidłowo ocenić wybrane detale. Błędy w ich doborze mogą być śmiertelne.
Niektórzy eksperci uważają, że na pojedyncze maszyny wystarczy blacha o grubości od 1 do 1,2 cm, np. jeśli chodzi o stół do krojenia. Inni specjaliści wychodzą z tego, że zawsze potrzebne są części o dużej grubości, nawet w przypadku niewielkich fragmentów konstrukcji. Istnieje również opinia, że masywne części klejone ze sklejki średniej grubości skuteczniej tłumią szkodliwe drgania przy okazjonalnych drganiach. Ale prawdziwi mistrzowie zawsze preferują względy niezawodności i bezpieczeństwa. Dlatego starają się jak najlepiej wykorzystać arkusze sklejki o grubości 19 mm lub większej, pomimo surowości i znacznych cen.



Ale nie powinieneś skupiać się tylko na jednej grubości. Konieczne jest uwzględnienie rodzaju oryginalnego drewna. Drewno iglaste jest lżejsze i bardziej miękkie, stosuje się je głównie na mniejsze węzły. Okleina liściasta jest droższa, a mimo to jest częściej stosowana. Ale różnice w składzie chemicznym klejów i poziomie odporności na wilgoć praktycznie nie odgrywają roli, w większości przypadków wystarczy sklejka klasy FC.
Ważniejsza jest kategoria oklein. Wzrost liczby sęków grozi pękaniem i rozwarstwianiem. Doświadczeni profesjonaliści starają się wziąć arkusze drugiej klasy i wyższej. Nie powinieneś próbować kupować bardzo taniego surowca. Doprowadzenie go do wymaganych parametrów w warunkach rzemieślniczych jest prawie niemożliwe.
W pełni oszlifowane elementy są również łatwiejsze do klejenia.

Za optymalny model do rękodzieła można uznać maszynę do sklejki 4 w 1. Konstrukcja ta zakłada użycie pudełka o wymiarach 54x32x88 cm i stołu 65x98 cm.Sklejka na te części ma odpowiednio 10 i 18 mm grubości. Przekrój tarczy szlifierskiej zwykle wynosi 18 cm. Do pracy na drewnie potrzebny jest inny aparat, typy różnią się znacznie, a mianowicie:
- piłowanie na podstawie ręcznej piły tarczowej;
- puzzle;
- za pomocą wiertarki;
- uniwersalny model, odpowiedni do zawieszania różnych przystawek.



Opcje domowej roboty
Całkiem możliwe jest wykonanie porządnej tokarki na bazie sklejki. Do pracy oprócz samego materiału potrzebne będą następujące elementy:
- klej;
- piła tarczowa i piła ukośna;
- ołówek lub marker, linijka (do znaków);
- zaciski mocujące;
- łożyska, farba, śruby, śrubokręt;
- metalowa płyta, silnik elektryczny i koło pasowe;
- szereg innych szczegółów.


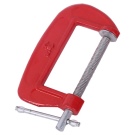



Do uformowania podstawy maszyny używa się sklejki o grubości 1,2 cm. Po wycięciu i sklejeniu półfabrykatów krawędzie są doczołowe, a rowki służą do montażu stojaków. Wrzeciennik jest również wykonany ze sklejki, konieczne jest wywiercenie w nim otworu na łożysko. Niektóre nakrętki i podkładki mogą być przydatne do klejenia. Szerokość platformy i części prowadzącej muszą się zgadzać, a dobrze wykonana platforma z zaciskami porusza się swobodnie w dwóch płaszczyznach.
Nie inaczej jest w produkcji konika i wrzeciennika. Oboje wymagają specjalnej ochrony. Napęd należy zamontować na płycie połączonej z podstawą zawiasem. Aby wykonać wrzeciono, musisz przyspawać dwie nakrętki w podkładce, a następnie zrobić „zęby” w nakrętce. Maszyna musi być pomalowana.


Oczywiście możesz również zrobić wiertarkę ze sklejki. Ponieważ jest on zwykle przeznaczony do stosunkowo małych elementów, można stosować arkusze sklejki o grubości 1 cm.Wszystkie części muszą być dopasowane tak ciasno, jak to możliwe, aby nie było widocznych wizualnie pęknięć. Ważne: materiał arkuszowy nie toleruje dużych obciążeń mechanicznych, więc łączenie części na gwoździe i wkręty byłoby złym pomysłem, można użyć tylko kolców i rowków, a czasami kleju PVA dla maksymalnego utwardzenia.
Jeśli planujesz wiercić inne wykroje ze sklejki za pomocą maszyny do sklejki, musisz zapewnić miejsce na wyłożenie kolejnego arkusza. W przeciwnym razie przetworzone produkty mogą pękać, a nawet pękać. Kolorystyka wiertarek nie jest zbyt uzasadniona. Są narażone na bardzo intensywne wibracje, obciążenia termiczne i mechaniczne. Ale zastosowanie podkładu jest bardzo przydatne, szczególnie w warsztatach bez ogrzewania.
Możliwy jest również montaż frezarek CNC lub obrabiarek do drewna. Ścieżka części obróbkowej (podobnie jak w innych typach) jest obliczana w trzech osiach. Jeśli w warsztacie nie ma wystarczającej ilości miejsca, uniwersalne stojaki mogą służyć do przechowywania szerokiej gamy narzędzi. Zazwyczaj obszar roboczy to 60x90 cm przy skoku pionowym 25 cm.
Ale jeśli robisz trochę mniej, zwykle nie pojawiają się żadne problemy.


Istnieją dwa główne schematy urządzenia dowolnych domowych obrabiarek do sklejki. W jednej wersji stół się porusza, a portal pozostaje nieruchomy, w drugiej zmieniają się role. Pierwsza metoda upraszcza projekt, ale nadaje się tylko do bardzo małych stołów roboczych. Dlatego w praktyce znacznie częściej stosuje się podejście z ruchem portalu i bezruchem stołu. Ale nawet w drugim schemacie mogą istnieć szczególne warianty.
Przede wszystkim dotyczą zastosowania jednego napędu centralnego lub dwóch napędów bocznych. Wersja z 2 napędami jest odpowiednia dla stosunkowo nieporęcznych konstrukcji. Minimalizuje ryzyko przekrzywienia portalu względem prowadnic. Ponadto cały zespół ma doskonałą sztywność. Wielkość obrabianego obszaru jest zdeterminowana zadaniami do rozwiązania.
Im większa maszyna, tym droższa wychodzi, a poza tym łatwiej korygować błędy na małych modelach.



Często uważa się, że geometrię portalu, proporcje odległości między osiami a prowadnicami roboczymi, szczeliny między łożyskami można obliczyć tylko biorąc pod uwagę wytrzymałość materiałów i precyzyjną mechanikę. To w dużej mierze prawda, ale podstawowe punkty są dostępne nawet dla niespecjalistów, a mianowicie:
- zmniejszenie prześwitu nad stołem zwiększa sztywność konstrukcji;
- osie powinny być również sztywniejsze i niezbyt długie;
- jeśli to możliwe, poszerzyć szczelinę między prowadnicami wzdłuż osi X, aby zmniejszyć nieprawidłowe skręcenie;
- środek ciężkości portalu musi odpowiadać punktowi, w którym znajduje się frez, a jednocześnie znajdować się między łożyskami osi Y (z tego powodu rozpórki pionowe są często wygięte do tyłu);
- wymagane jest stosowanie tylko śrub z nakrętką kulkową, które dają najmniejszy luz;
- śruba musi być wyposażona w parę niezależnych łożysk i połączona z silnikiem za pomocą elastycznego sprzęgła (wówczas uzyskuje się równowagę prostoty i jakości)
- montaż wszystkich kluczowych części można przeprowadzić na kolcach skrzynkowych (jest to o wiele bardziej estetyczne niż wybrzuszające się we wszystkich kierunkach nakrętki).

Jak to zrobić samemu?
Nie ma potrzeby szukania gotowych rysunków. Możesz budować na schematach maszyn metalowych. Zresztą każdy taki produkt jest wyjątkowy i zoptymalizowany pod konkretne zadania, na osobiste potrzeby właścicieli. Należy jednak zwrócić uwagę na przykładowe zdjęcia. Maszyny do sklejki można prawidłowo wykonać tylko za pomocą wysokiej jakości elektronarzędzia. Jeśli arkusze o grubości do 1 cm są cięte wyrzynarką, to grubsze są zwykle przetwarzane za pomocą piły tarczowej lub tarczowej. Jednak zaawansowane wyrzynarki poradzą sobie również z cięciem arkuszy sklejki o grubości do 2 cm.
Frez ręczny pomoże wybrać rowki i otwory. Poruszaj narzędziami płynnie, aby zminimalizować odpryski. To samo osiąga się za pomocą zwykłej taśmy. Po ostatecznym montażu wszystkie powierzchnie i powierzchnie muszą zostać przeszlifowane. Jako glebę możesz użyć mieszanki wody i PVA w równych proporcjach.



Możesz dowiedzieć się, jak zrobić szlifierkę taśmową ze sklejki własnymi rękami z poniższego filmu.
Komentarz został wysłany pomyślnie.